钢厂设备防腐涂漆的最新技术
1前言
钢厂的许多设备,如装卸铁矿石和煤等原料的装卸机和输送皮带,还有运出钢铁产品的港口起重机以及输送各种能源介质的输送管道和燃气储罐等,都是在遭受海滩飞来的盐分和腐蚀性气体等腐蚀的严酷环境下使用的。为了对钢厂的这些基础设施设备进行防腐维护,以前是定期重新刷漆。但是,在设备的防腐维护工作中常常不得不面临以下诸多问题,例如:如何对涂漆层老化状况进行点检,如何确定重新刷漆的时间,如何按计划确保重新刷漆所需的费用等。
另一方面,从企业的社会责任来说,预防设备事故的发生已越来越重要,决不能发生因腐蚀而引起的设备事故。钢厂设备维护部门在采用最佳防腐技术,防止因腐蚀引起设备事故方面起着重要的作用。
基于上述原因,对钢厂设备采用最佳防腐涂层既可以使设备稳定运转,又可以降低设备的使用寿命周期成本(下称“LCC”),因此与防腐保护有关的设备管理水平和防腐涂层技术得到不断的发展。新日铁住金公司制定了各种适用于钢厂设备防腐涂层技术的标准,并根据需要进行更新,同时对设备维护人员和生产技术人员进行腐蚀与防腐蚀技术的教育,而且开发了独有的设备防腐技术。
本文就钢厂设备防腐保护而开发的涂层诊断技术和防腐涂漆技术进行介绍。
2涂层诊断技术
2.1表面形状的三维计测
在钢制路桥的维护管理中,一般是通过目视点检对涂
层老化情况进行诊断。在钢结构涂层调查手册中,作为目视调查的项目有生锈、剥落、变退色和污损等,而且对于腐蚀的发生程度是根据生锈的面积(%)进行评价。也就是说,它是根据发生黑点锈部分的面积率来判断腐蚀发生的程度。目视点检法对钢厂设备防腐保护来说也是很重要的。但是,根据点检结果判断是否重新刷漆和重新刷漆的时间是不容易的,这对于设备维护人员来说是一个很大的问题。因此,为使设备维护人员能准确把握涂层老化的现象,并将设备点检结果应用于设备管理,必须对设备维护人员进行有关腐蚀与防腐蚀技术的教育。
在腐蚀与防腐蚀技术教育过程中,为有助于设备维护人员对涂层老化现象的把握,采用盐水喷雾试验法(下称“SST”)来加速试样涂层的腐蚀速度,并采用表面形状三维计测技术对腐蚀状况进行计测试验。测定装置由激光距离仪和XY工作台构成。图1示出该测定装置的测定结果。图1(a)表示试样可测定的范围,(b)和(c)表示采用表面形状三维计测技术获得的涂层表面的等高线图和俯视图。由图可知,在(a)图中看到的黑点锈就是在(b)和(c)图中鼓起高度达数百微米的黑点。图2用照片和三维俯视图示出SST随时间变化产生锈的状况。根据这些测定结果可知,所谓涂层老化现象是指涂料在涂层表面发生鼓起后慢慢增大,不久便从鼓起的前端产生流锈,然后污损周围这样一个过程。由于涂层会从钢表面剥落,因此鼓起的涂料内部会成为不利于防腐的部分。鼓起的涂料内部产生的腐蚀被称为“涂层下的腐蚀”,由此产生的锈和锈汁会导致流锈的产生。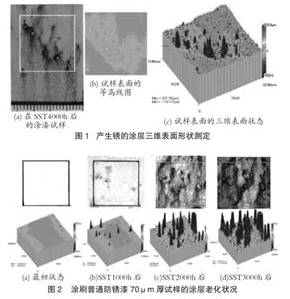
本试验通俗易懂地揭示了涂层老化的发生过程,由此可知锈的发生面积(%)也就是涂料鼓起的面积率。据此,可以设定涂料鼓起高度的阈值,在表面形状三维计测装置内计算超过阈值高度部分的面积,从而可以计算出锈的发生面积(%)。可以说,在实验室内采用本方法能有效诊断出试样涂层老化的状况。但是,由于表面形状三维计测装置的测定范围有限,只有大约20mm的方形范围,因此不得不说它难以对设备进行现场涂层诊断。
2.2电离透射电阻测定法
为有效进行涂层的现场诊断,对耐大气腐蚀性钢生锈诊断用的电离透射电阻测定装置(下称“RST”)进行了改良。具体的改进内容就是将可测定的薄膜电阻由原来的最大2G扩大至20G。由此使以前只能测定耐大气腐蚀性钢生锈电阻值的装置变为可以测定防腐涂层电阻值的装置。
在等效电路中示出了涂层电阻(RR:下称“RST值”)。测定原理为,将小于特定频率数的数毫安交流电流从充满电解液的两个活塞中流过,计算出RST值(?)。在刚涂漆后的完整涂层中,防腐涂层的RST值大于最大测定值的20G,但随着涂层的老化,涂层上会产生很多鼓起,RST值会变为数千欧。
作为实际测定例子,介绍了2012年11月钢厂港口起重机涂层的诊断结果。表1示出各部位的测定结果和涂层表面的照片。实际设备的RST值与根据目视点检和涂层外观判断的老化状况较一致。也就是说,处于陆地上的设备上部装置粘附的从海上吹来的盐分容易被雨水冲掉,其RST值大于20G,而悬臂内侧涂层上粘附的盐分很多,且不容易被雨水冲掉,其RST值非常低,大约20k,因此发生了腐蚀。由此可知,RST值有助于实际设备的涂层诊断,其特征是通过诊断获得RST值的数据有助于对设备进行定量维护。另外,设备所有部位的涂层并不是同时同等程度老化,部分处于严酷腐蚀环境的部位会先发生老化,根据RST值可以确认不同部位所产生的不同老化现象。
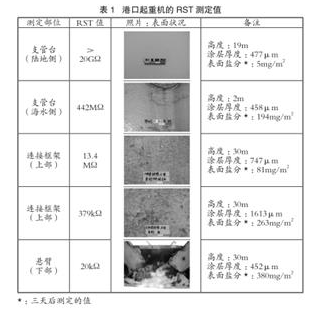
根据以上所述,希望今后能利用RST值的定量数据制定防腐维护计划,例如,为减少重新刷漆的费用,可对不同的部位采取不同的涂漆办法,或只对涂层老化明显的部位进行重新刷漆等。
3防腐涂漆技术
3.1厚浆型涂漆法
关于钢结构的涂漆,以前作为防锈涂料通常是以含铅的油性涂料(铅丹防锈漆)作为底漆,以合成树脂涂料(长油性邻苯二甲酸树脂涂料)作为二道墁抺漆和面漆,但从1990年左右开始改为以长久耐用性好的变性环氧树脂涂料作为底漆,以聚氨酯树脂涂料作为二道墁抺漆和面漆。这表明了如果要重视长久耐用性,就应当将钢制道路桥梁涂漆指南中所列出的A涂漆方法(轻防腐涂漆方法)替换为C涂漆方法(重防腐涂漆方法)。根据这种钢制道路桥梁涂漆技术的发展趋势,为实现钢厂设备防腐涂漆的长寿命化,新日铁住金公司对公司内的设备防腐涂漆技术手册进行了修订。即,增加了使用变性环氧树脂涂料作为底漆的涂漆方法。但是,钢制道路桥梁的C涂漆法除了要进行涂漆预处理外,还要进行6次涂漆,涂漆的成本非常高,因此开发了适用于钢厂设备防腐用的廉价的重防腐涂漆方法。
图3(c)示出开发的厚浆型涂漆法。该涂漆法是一种经济型涂漆方法,其涂层的厚度比C涂漆法(图3(b))和ISO12944-5中的海洋环境用C5-M方法(图3(d))的厚,且漆的涂刷次数少。另外,厚浆型涂漆法使用的变性环氧树脂涂料就是把防腐性能好的变性环氧树脂涂料改为厚浆型,底漆涂刷3次就可达到300μm厚。作为整个厚浆型涂漆法,只增加1层聚氨酯面漆,整个涂层厚度就可达330μm。
本文就改进的厚浆型变性环氧树脂涂料的概况进行介绍。本涂料涂刷一次就可达100μm厚,因此适当添加了特定尺寸比的鳞片状颜料,刷漆时在湿式状态下反复涂刷就可形成厚涂层。图4示出本厚浆型涂料涂刷一次的防腐性能和A涂漆法防腐性能的比较。根据SST2000小时后,从横切部剥落的涂层宽度比较可知,采用A涂漆法时整个涂层面发生了剥落,而采用厚浆型涂漆法时,涂层的剥落宽度最大为2.5mm,表明具有非常好的防腐性能。
目前,上述厚浆型涂漆法已成为钢厂室外设备的标准涂漆方法,厚浆型涂料已成为推荐的防腐涂料。
3.2能源管道内面的涂漆
在钢厂,COG(焦炉煤气)和LDG(转炉煤气)等能源输送管道的铺设长度高达数十千米以上。这些管道将各种燃气等能源输送到钢厂各车间。但是,这些管道内部会因气体或冷凝水的腐蚀性而慢慢被腐蚀,经过大约30年以上的时间会发生管道穿孔问题。例如,COG管道会因COG中含有的硫化氢和冷凝水中含有的亚硫酸离子等的影响,而形成含硫的层状腐蚀生成物。另外,LDG管道会因气体或冷凝水中含有的碳酸气体而产生腐蚀。因此,钢厂的能源输送管道内面必须采用防腐技术来防止管道内面产生腐蚀。基于此因,研究了采用涂漆的方法来防止管道内面产生腐蚀的技术。在这种情况下,防腐涂料必须具有不会被气体或冷凝水中含有的各种化学物质侵蚀的耐用性(耐药性)和可阻断环境腐蚀的性能。为此,开发了分子结构强、可现场施工且常温硬化的玻璃转变温度(Tg)高的无溶剂环氧树脂涂料。为确认开发涂料的防腐性能,对各种涂料的防腐性能进行了裸露试验比较。作为试验结果,图5示出涂漆试样在COG管道冷凝水中浸渍6个月后,对涂层断面进行分析的结果。采用断面照片和EPMA(电子探针显微镜分析仪)对耐药性的溶剂涂料(a)和开发的无溶剂涂料(b)的S渗透分布状况进行了比较。由结果可知,开发的涂料能有效抑制S从涂层表面渗透。该开发涂料目前已用作各种能源输送管道内面和钢制烟囱内面的防腐涂料。
3.3支管台防腐
钢厂铺设的各种能源输送管道是通过设置在支柱上的管道支架(下称“支管台”)支撑着。支管台由下部的钢制支撑台和上部的钢制管道卡圈构成。在支撑管道的状态下,支管台与管道之间会形成缝隙。具体说来就是管道与支管台之间的缝隙、管道与钢制卡圈之间的缝隙,在这些缝隙处有时会产生腐蚀。
松开钢制卡圈后,对因卡圈下的缝隙腐蚀而产生的锈进行了观察。可以认为卡圈下的缝隙腐蚀导致的生锈现象是由于雨水渗透到缝隙后不容易干燥而引起的。有时最终会导致管道发生穿孔,因此必须进行防腐处理。作为防腐处理办法,就是从支管台卸下管道,对缝隙部进行涂漆,但这不仅要花费大量的费用,而且在卸下管道时有可能发生煤气泄漏,只能在停气的情况下卸下管道。由于钢厂的生产是24小时昼夜不停,一旦停止煤气的输送会对钢厂的生产计划产生重大不良影响,所以希望有一种能在不卸下管道的情况下进行防腐处理的方法。
因此,开发了支管台防腐处理方法,即在管道与支管台或与钢制卡圈之间的缝隙中压入容易渗透的低黏度氨基甲酸乙酯树脂涂料的方法。图6示出压入施工的示意图。在压入低黏度氨基甲酸乙酯树脂涂料时,除了涂料注入部和排出部外,要预先用密封剂对支管台和钢制卡圈的两端进行密封固定,使涂料能渗透到整个缝隙中。低黏度氨基甲酸乙酯树脂涂料在渗透后的硬化过程中会捕捉缝隙内的水分。因此,即使缝隙内的水分渗入涂料中也没关系,依然能确保防腐效果。
该防腐处理法除了可以应用于钢厂的支管台外,还可用于轧机底部和底板间的缝隙防腐以及钢制桥梁狭隘部的防腐处理,且应用范围不断扩大。
3.4轻微除锈涂漆法
关于涂漆前的表面清理,一般是采用一种除锈(喷砂清理)或两种除锈(动力设备)方法进行除锈清理。具体说来,标准的清理方法是按照ISO8501-1制定的Sa21/2或St3进行表面清理。但是,在对腐蚀相当严重的煤气管道或煤气储罐外部进行涂漆时,如果采取普通的表面清理方法,有可能发生穿孔并导致煤气发生泄漏,因此基本上是停气后用氮气清除内部气体。但是,如支管台防腐中所述的那样,如果能在不停气的情况下进行涂漆,涂漆操作就会变得简单,成本也会降低。因此,研究了只留下薄薄一层锈的表面除锈清理(下称“轻微除锈涂漆法”)便可确保某种程度的防腐性能的涂漆法。
所谓轻微除锈涂漆法就是在除锈作业时留下大约100μm厚的锈层。表2示出SST3000小时后的防腐性能的比较试验。如果留下锈层的厚度在100μm以下,可以使用具有在锈中渗透性能的特殊底漆,如果在其底漆上涂刷普通厚浆型涂料,即使在SST3000小时后也能确保防腐性能。这是因为在留下的100μm以下的薄锈层中,特殊底漆能完全渗透到锈层中,抑制留下的锈发生腐蚀所致。
轻微除锈涂漆法仅适用于能源输送管道或煤气储罐的内部气体没有放出情况下的涂漆处理。另外,试验表明,在留下锈层的厚度大于100μm的情况下或特殊底漆的厚度大于标准涂层厚度的情况下,无法获得防腐性能,如表2中的No.1所示。
本方法应用于实际涂漆施工时,在轻微除锈清理过程中对留下锈层的厚度进行了测定,以确认留下锈层厚度在100μm以下。还有就是采用喷水喷砂法进行除锈。例如,对煤气储罐的外面涂漆,采用喷水喷砂除锈法可有效进行大面积除锈,不仅除锈成本低,而且不会发生动力工具除锈时产生火花而引起火灾的危险现象。但是,轻微除锈涂漆法在SST3000小时以上的长久耐用性尚未得到确认,因此根据具体情况,它仅限于无法采用普通表面除锈作业的情况下使用。
4结束语
本文介绍了可应用于钢厂基础设施设备的涂层诊断技术和防腐涂漆技术,并以港口起重机、能源输送管道、支管台和煤气储罐为例,介绍了各种涂层诊断技术和防腐涂漆技术的应用。以下就其内容进行简要概括。
1)作为涂层诊断技术之一,提出了采用表面形状三维计测法进行涂层诊断的方法,确认了涂层老化就是涂层表面发生鼓起并增大的现象。
2)作为可应用于现场的定量涂层诊断方法,提出了采用电离透射电阻测定装置(RST)测定涂层电阻的方法。作为应用事例,列举了港口起重机涂层RST值的测定,确认了设备粘附盐分容易被雨水冲掉部分和不容易被雨水冲掉部分会发生不同的涂层老化。
3)靠海钢厂室外设备的防腐涂漆法要求涂料必须具有很好的耐久性,因此可以厚浆型变性环氧树脂涂料作为底漆实施厚浆型涂漆法。
4)作为能有效防止钢厂能源输送管道发生内面腐蚀的防腐涂漆料,可以使用无溶剂型高Tg环氧树脂涂料。
5)作为应对能源输送管道支管台产生缝隙腐蚀的措施,提出了在缝隙中压入低黏度氨基甲酸乙酯树脂涂料的防腐处理方法。
6)在能源输送管道和煤气储罐的外部涂漆施工过程中,作为能够不置换内部煤气且不会引发火灾危险的除锈涂漆施工法,提出了轻微除锈涂漆法和喷水喷砂除锈法。
如上所述,本文介绍了几种涂层诊断技术和防腐涂漆技术。但是,除此之外,钢厂还有许多必须进行防腐保护的大型基础设施设备。钢厂设备防腐工作还存在着许多未解决或正在研究解决的问题。例如,烟囱内面在高温环境下的防腐、处于海水环境或地下环境中设备的防腐、水中钢筋混凝土的防腐和加固等。另外,还必须保存点检数据,建立有助于设备维护管理计划实施的系统。因此,所谓钢厂防腐维护,是一个涉及技术领域非常广、需要多部门承担职责相互协作,并不断努力的综合性设备管理工作。今后,新日铁住金公司和新日铁住金防腐公司还将与相关部门及相关公司密切配合,为实现钢厂设备防腐维护工作取得更大成绩而不懈努力。 (廖建国)