摘要:简要介绍转炉煤气干法净化回收系统的工艺流程,结合实际生产数据从工艺控制、设备操作及组织管理等多方面分析影响煤气回收的因素,并提出切实可行的提高煤气回收率的方法,为钢铁企业创造良好的经济效益和社会效益。
0引言
转炉烟气是转炉炼钢的副产物,主要成分是CO,具有较高热值,经过净化回收的转炉煤气可作为优质燃料,是钢铁企业生产重要的二次能源。转炉煤气可单独作为工业窑炉的燃料使用,也可和焦炉煤气、高炉煤气等配合形成各种不同热值的混合煤气使用。对转炉煤气回收利用是国家产业政策的要求,也是节能降耗及实现“负能”炼钢的需要。
近年来,干法净化回收系统在新建或改造转炉炼钢的烟气净化回收项目上被越来越多的采用,随着系统设备的升级改造、优化以及生产管理水平的提高,煤气回收率也在不断提高,但目前转炉煤气的回收利用仍然存在薄弱环节。
转炉煤气回收不仅受炼钢的工艺、设备水平的影响,更与日常管理技术息息相关。提高转炉煤气的回收率,不仅能降低炼钢生产成本,为实现“负能“炼钢打下基础,而且极大的降低了污染物排放总量,满足了环保要求。
本文以国内某钢厂120吨转炉炼钢干法净化回收系统为例,简要介绍转炉煤气净化回收系统的主要工艺以及烟气成分的变化过程,重点分析转炉煤气的回收的影响因素,同时提出具体措施,充分发掘系统潜能,安全高效的提高转炉煤气的回收水平。
1转炉煤气干法净化回收系统
1.1转炉煤气干法净化回收系统工艺
转炉炼钢过程中产生的高温烟气首先由活动烟罩捕集,然后经过汽化冷却烟道,在回收热能的同时对烟气进行初次降温。汽化冷却烟道出口温度约为900℃。
转炉煤气干法净化回收系统采用蒸发冷却的方式进行烟气的二次降温,同时捕集粗颗粒粉尘。冷却和初除尘后的烟气进入静电除尘器进行精除尘,为满足电除尘器工作的温度条件,静电除尘器入口温度控制在150~180℃范围内。
冷却后的烟气进入静电除尘器进行精除尘,煤气冷却器出口烟气含尘含量≤10mg/Nm3,放散烟囱出口气体粉尘含量≤15mg/Nm3。
除尘后的烟气经风机送至切换站,实现煤气放散或回收的快速切换。为适应转炉烟气的变化,风机采用变频调速,以达到流量调节。在切换站前设有气体分析仪可根据分析仪检测的一氧化碳含量来控制放散和回收杯阀的切换,当烟气中氧含量及一氧化碳气体含量达到回收条件(CO含量大于25%,氧气含量小于1%)时,通过切换站的回收杯阀进入煤气冷却器,经喷淋冷却至一定温度并通过管网送入煤气柜。不合格的煤气或合格煤气气柜拒绝回收时,则通过切换站的放散杯阀进入放散烟囱点火放散。
转炉煤气干法净化回收系统工艺流程见图1。
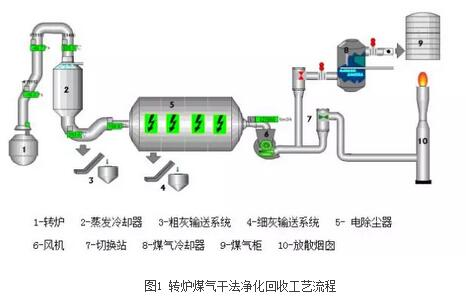
1.2转炉冶炼工艺烟气状况
转炉炼钢过程中,铁水中的碳在高温下和吹入的氧生成CO和少量CO2的混合气体,成为转炉烟气,转炉烟气净化后称为转炉煤气。转炉烟气的发生量在一个冶炼过程中是变化的,所以转炉煤气的量也随之变化。
转炉冶炼初期由于受到铁水温度低、硅锰元素的氧化等条件限制,铁水中的碳没有被大量氧化,CO与CO2的含量较低(图2),冶炼120~180S后随着硅锰氧化反应结束,铁水温度上升,碳元素开始大量氧化,CO与CO2的含量开始快速上升,冶炼中期碳氧进行剧烈反应,CO与CO2的含量稳定在较高水平,冶炼后期,随着铁水中碳含量的下降,产生的烟气量也随之减少。大量空气进入烟道内与CO发生燃烧,CO含量降到最低。转炉烟气成分的变化曲线见图2。
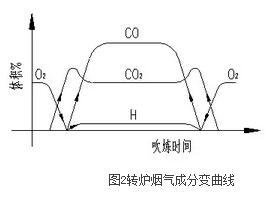
2国内某钢厂120吨转炉煤气回收研究分析
某炼钢厂120吨转炉在投运初期,煤气柜尚不具备回收条件,净化后的煤气全部点火放散,转炉活动烟罩未实行升降罩操作,炉口微差压亦未投入使用,风机根据炉口返烟情况手动设定调节,吹炼周期内CO含量普遍偏低。实现煤气回收后,为提高煤气回收率,分别从转炉活动烟罩的降罩操作、炉口微差压数值设定及风机PID控制水平、汽化烟道氮封系统调整、生产组织和设备管理等几个方面进行了分析研究和调整改进。
2.1活动烟罩降罩操作
在转炉吹炼初期,为保证产生的CO能在炉口完全燃烧成CO2,以避免泄爆情况的发生,不实行降罩操作,当氧枪在等待位以下或氧气阀完全打开后,持续90秒再将转炉活动烟罩降至下限位置。活动烟罩升降示意图见图3。
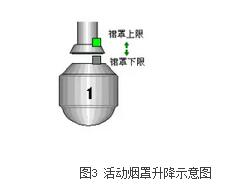
本次对比系统其它可能存在影响因素均未作优化调整,仅实现降罩操作,降罩操作前后,转炉煤气中CO的含量变化对比曲线见图4:
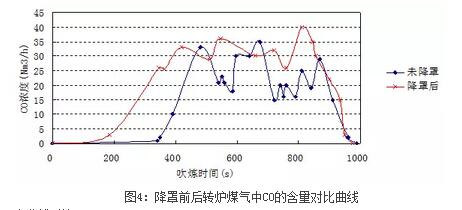
由曲线对比可见:
未降罩时:在吹炼430秒左右,CO含量升至25%,约900秒以后CO降至25%以下。在430秒至900秒之间CO含量最低为14%,此区间平均含量约为25%。CO含量曲线变化比较剧烈,在区间内CO含量多次降低至20%以下。
降罩后:在吹炼350秒左右,CO含量升至25%,约900秒以后降至25%以下。在350秒至900秒之间CO含量最低为25%,此区间平均含量大于30%。CO含量曲线变化相对平缓,以30%为中心上下波动,区间内最低值大于25%。
经对比分析可知,转炉炼钢时采取降罩操作,吹炼阶段CO含量有显著提高,且降罩后CO含量升至25%的时间提前约80秒。可见转炉炼钢的降罩操作对提高转炉煤气的回收率及回收质量均有良好效果。
2.2炉口微差压数值设定及风机PID控制
为防止大量空气吸入烟道,造成转炉烟气中CO在高温下燃烧成CO2导致CO含量降低,从而降低煤气回收质量。在烟道入口及烟道末端两个位置均装有用于测量烟道压力的测压环管,通过差压变送器所测的差压值PLC进行PID运算,输出风机转速设定值,并不断调整修正风机转速,最终将炉口压力控制在微正压状态。
炼钢过程中,将炉口微差压控制值分别设定为-10Pa和+30Pa,观察不同炉次炼钢时转炉炉口状况并分析风机转速的变化情况。图5为炉口微差压不同设定值下的风机转速变化曲线。
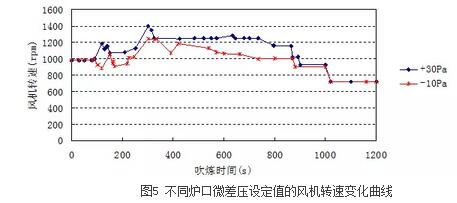
当口微差压值设定为+10Pa时,炉口处于微正压状态,炉口如有如无的少量烟气被二次除尘所抽走。当口微差压值设定为-30Pa时,炉口表现出明显的抽力强劲,大量空气被抽入汽化烟道进入干法回收系统。
分析图5可知,上部曲线的炉口微差压值设定为+10Pa,整个炼钢过程中风机瞬间最高转速约1220rpm,炼钢中期转速平均约1050rpm。下部曲线的炉口微差压值设定值为-30Pa,整个炼钢过程中风机瞬间最高转速达1400rpm,炼钢中期转速平均约1220rpm。显而易见,当炉口微差压设定数值发生变化时,风机转速曲线亦跟随发生变化。炉口微差压设定的负值越大,风机转速越高,吸入的空气则越多,经过燃烧反应,大大降低烟气中CO的含量,直接导致可回收时间的缩短,可见炉口微差压的设定值对煤气中的CO含量及回收率均有影响。
将炉口微差压设定在微正压的状态,通过精准的控制计算,使风机转速运行在最佳的转速状态,确保提高转炉煤气回收率。
2.3汽化烟道的氮封系统
某钢厂在煤气回收初期,煤气柜分析数据显示氮气含量高达45%,通过不同压力下的调整分析发现,当氮封压力大于0.3MP甚至更高时,氮气流会对炉口产生冲击,造成炉口气流紊乱,烟气外溢。为避免烟气外溢,操作人员往往会首先提高风机转速,于是大量外部空气被吸入,空气中的氧不仅造成烟气中CO燃烧,而且空气中的氮气和氮封系统的过量氮气同时进入烟气中,大大增加了烟气中氮气含量,造成回收煤气品质降低。
在采取转炉降罩操作及炉口微差压调整后,同时对汽化系统活动烟罩、下料口及氧枪口氮封系统进行调整。经过反复试验发现,当氮封压力低于0.25MPa时,既能保证炉口平稳杜绝烟气大量外溢,又可保证密封效果。最终将煤气中氮气含量控制在33%左右,大大提高了回收煤气品质。
2.4生产组织和设备管理
除了转炉炼钢工艺、原材料条件及炼钢操作水平的影响,由于转炉生产的周期性,煤气回收与转炉冶炼节奏、煤气柜储气容量等均密切相关,因此生产组织的良好与否对煤气回收率的影响也至关重要。
加强设备的日常维护,出现故障及时检修,可有效延长设备使用周期,减少因设备故障停炉而影响连续生产,从而有利于提高煤气回收率。尽可能统一协调,将转炉系统、干法净化回收系统以及煤气柜的检修工作安排在同一个时间进行,以减少对转炉炼钢连续生产的影响。
3结束语
通过活动烟罩的降罩操作、炉口微差压数值设定及风机PID控制水平、汽化烟道氮封系统调整、生产组织和设备管理等几个方面的分析调整和改进操作,煤气回收CO含量及煤气回收率均有显著提高。
本文通过对比分析研究`,提出具体措施以提高转炉炼钢过程中转炉煤气中CO的浓度,增加煤气回收率,对炼钢厂实际生产中提高社会效益和经济效益具有重要的指导意义。