马钢 4 000 m3 高炉提升上料能力控制实现
王成伟
(马鞍山钢铁股份有限公司 第三炼铁总厂,安徽 马鞍山 243000)
摘要: 马钢第三炼铁总厂 A、B 高炉先后于 2006 年投产,每天平均上料批次约 132 批,最高批次约 145批。通过调整矿槽及炉顶计算机控制程序,使高炉最大上料能力得到提升,减少故障亏料、塌料等状态下的赶料时间。同时,使高炉能够满足焦/矿/矿(C/O/O)、焦/矿/碎矿(C/O/S16)、中心加焦等特殊布料模式。通过提升上料能力,减少高炉炉况异常时的燃料比,使高炉具备特殊排、布料模式下的调节炉况手段。
关键词: 高炉;上料能力;布料;控制
0 引言
马钢第三铁总厂 A、B 高炉炉容均为 4 000 m3 ,采用单列式矿仓下料,矿石、焦炭、球团矿分别置于两侧,但经同一条 N2 皮带至 N1 皮带后装入炉顶,不设中间仓。矿石料仓布置亦与大部分高炉不同,焦丁及矿丁需要经过 N3 皮带机倒入中间仓,且两种物料共用 1 个料仓;而中间仓及球团仓布置于矿槽的尾部(远离高炉侧)。在高炉正常生产中,焦丁、球团按设定时间或重量精确平铺于料条前部指定位置。鉴于上述两种特殊情况,高炉从排料到物料到炉顶时间较长,并且每 2 批料间需要安全间隔,故此种模式下高炉上料能力较低。高炉炉顶采用串罐式无料钟炉顶系统,主线设备包括上罐受料系统、上料闸系统、下罐称重系统、均排压系统、下料闸系统、溜槽系统、探尺系统等。在高炉正常生产时一般会采用焦/矿,即 C /O 上料模式,在此种模式下焦炭一般按物理顺序依次排料。矿石系统分为烧结矿、球团矿、生矿、焦丁、小粒烧,每个料种按生产设定的重量、指定料条长度、指定位置排料,从而确保入炉布料在指定的炉内位置。
在高炉因设备故障无法正常上料而亏料、减风,或高炉炉况异常出现大的塌料时,高炉炉内料线急速下降,有时甚至达 4 ~5 m 深,高炉往往伴随着顶温骤然升高情况(正常顶温在200 ℃以下,当出现深亏料时甚至会飙升到 600 ℃)。这种情况下缩短赶料时间会直接造成高炉热量损失,从而影响高炉的燃料消耗;同时高顶温会加速炉顶下密封阀和密封圈等老化,煤气温度影响清洗效果等联锁反应。提升上料能力,精确排料、精准布料对稳定高炉炉况,降低燃料比具备重要意义,本文介绍一种提升上料能力、精准布料方法。
1 高炉上料能力提升实践
1. 1 上料能力现状
高炉上料能力主要取决于槽下上料能力及炉顶上料能力,二者需要相互匹配。一个正常上料周期是从炉顶下罐开始向炉内布料槽下开始排料,矿石与焦炭经 2#主皮带、1#主皮带后进入炉顶上罐(受料罐);待炉顶下罐排料结束阀门关闭且排压完成后开上罐料闸、上密封阀将物料倒入下罐;之后经过一、二次均压,待炉顶到设定料线溜槽完成上倾后再开始布料。
在上述过程中,槽下物料与皮带的起始距离、料条长度、两批物料之间的安全距离(保障炉顶可以正常受料、倒罐)、炉顶各阀门动作时间等均影响到整个过程的总体时间。实测炉顶实际等料线时间(按均压完成炉顶准备好后等料线到布料的时间)为 7 800 ~9 600 s 之间(2.18 ~2.67 h)。改造前在B 高炉108 t 矿批、22.5 t 焦批测试槽下上料能力 15批平均数据如下:图 1 中的矿石料条长度约 177 s(T1)、图 2 中的焦炭料条长度约 162 s(T2)、炉顶保证最小间隔时间 61 s(T3)。在此种模式下,槽下极限上料能力(以一个班 8 h 计算)为 8×60×60/(T1+ T2 + T3×2) =65.3 批;以标准的每班43 批料计算,上料能力Acx =65.3/43 =151.8%。
炉顶上料能力与各个阀门动作时间及料种设定的料制有关,正常情况下炉顶料制设定布料环数约为 15 环,即 112.5 s(T5),阀门动作时间总计约120s(T4)。故炉顶最大上料批数为8×60×60/(T4×2 + T5×2) =61.94 批;以标准的生产每班 43 批料计算,上料能力 Ald =61.94/43 =144.0%。
1. 2 上料能力提升分析
鉴于上述统计,槽下、炉顶极限上料能力分别为151. 8%、144%。但在实际生产中,槽下排料就绪后需要等待炉顶布料后才开始排料。因此,槽下提升上料能力重点是缩短料条长度;炉顶上料能力提升的关键是阀门动作时间及间隔,合理调整炉顶及槽下之间的安全时间、精确控制放料时间。
1. 3 具体实施方案
1. 3. 1 槽下系统
(1)矿石系统
槽下主要是集中缩短料条,目前 B 高炉矿石排料方式为轻载模式、球团为平铺模式,即烧结矿先排,后续烧结矿其料尾到信号按物理位置依次排料。当烧结矿排过设定重量的某一百分数后焦丁开始排料,当烧结矿料头发出设定一定时间后球团开始排料,其他球团矿仓按球团料尾依次排料;当球团料头到生矿仓后生矿开始排料,其他仓也按生矿料尾依次排料。这样最多有 4 段料平铺,实际料条中烧结矿料条置于最底层且料条长度最长。因此,为缩短烧结矿料条,计算机程序中按照 2 个仓的物理位置及距离跟踪物理位置,保证物料均匀地置于皮带中间且不漫料。在实际使用中,前一个仓在放料结束后,程序需要检测料仓的重量变化,当没有料流后按照仓间隔计算时间控制下一个料仓排料。而下一个物理位置料仓需要计算机发出指令,现场电气接触器动作,从而电机得电带动现场闸门。现场查看物料在 2 个料仓连接处往往出现空挡、物料少情况,所以可在计算机中通过修改控制程序调整 2 个料仓间隙,从而达到缩短料条长度的目的,同时现场将烧结矿仓闸门开度调整到最大。
(2)焦炭系统
槽下焦炭仓总计 8 个,按焦炭常用料种分为新干焦、老干焦、湿焦,分别分布于料仓的后段、前段及中段,在使用中按物理位置从 8B 仓到 1B 料仓顺序排料。一般湿焦仓仅有 1 个,且放于中部,现场实际料仓闸门在全开情况下焦炭物料仅占堆积不足一半的皮带截面。此种情况考虑将新干焦、老干焦料 3个仓进行平铺,2 个仓同时排料。
1. 3. 2 炉顶系统
炉顶系统中按照 PW 厂家提供参数时间,上料能力在 170%左右;各阀门动作时间较短,且无阀门间保护延时。在使用中为保护上密、下旋转机构等重要备件及现场环保等因素,对液压系统油压及阀门液压流量进行调整。同时,炉顶正常在开下料闸角度大于 30°时排料,将排料时间提前到提探尺排料仅此更改每罐料,可提升 11 s 时间。所有炉顶在提升上料能力时主要调整次要阀门动作时间及安全时间、更改槽下炉顶安全监测间隔时间。
1. 4 试验与测试
1. 4. 1 槽下调整
针对上述改造方案,对我厂 B 高炉逐步进行改造,首先调整烧结矿排料间隔时间,现场将 2A -10A 共9 个仓缩短2 s 时间,现场测试料条效果较明显。实测现场矿石物料基本头尾相接无明显空挡,但在连接处仍有窄料条。随即将时间再次调整 1 s,测试现场物料基本按要求重叠且料条宽度基本一致,已达到预期效果。焦炭仓将现场闸门开度调整到最大后,将 8B - 2B 共 7 个仓间隔时间缩小 3 s,并记录 15 批时间。实侧平均料条长度为 14. 1 s,矿石长度为 136. 4 s,详见图 3、图 4。
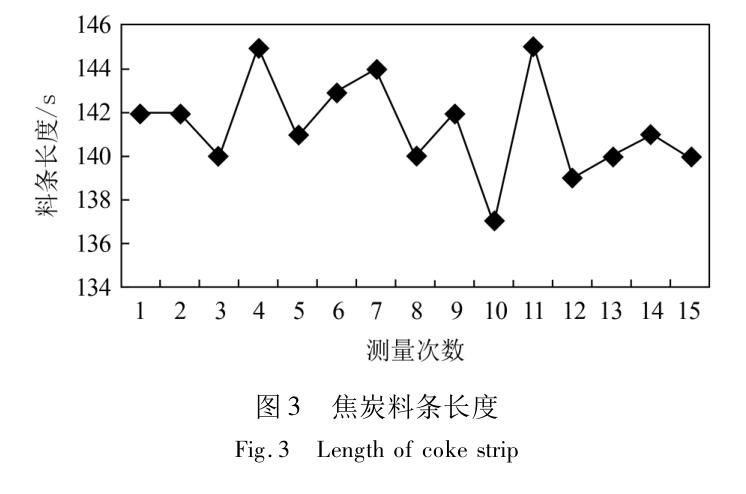
焦炭在第一次调整后皮带物料基本头尾相接,料宽基本一致;但焦炭在皮带上料层厚度仍有调整余地,按预定方案将焦炭分料种平铺。经过第二次调整后测试15 批物料,实测料条长度降为88. 4s,效果显著,如图 5 所示。
1. 4. 2 炉顶调整
首先对炉顶延时信号进行调整,其次将排料改为提探尺。实测阀门动作时间及指令发出时间缩短19 s 左右,同时将槽下及炉顶联系料仓满信号检测时间缩短 10 s。
1. 5 实施效果
对实测数据进行分析,目前槽下上料能力计算为83.04 批,按每班43 批次计算为193%;炉顶上料能力为67.45 批,按每班 34 批次计算为 156.8%。故槽下及炉顶上料能力分别较之前提升了42% 与17%,实际在使用中每个班次等料线时间为10 400~12 860 s之间,较调整前效果显著。
调整后因高炉炉况波动曾出现 1 次较大的塌料,其中最深尺料线达 4. 3 m。按调整前上料能力需近2 h 可恢复料线,实际仅经1 h 15 min 即达到设定料线。同时,2016 年 11 月开始测试分割布料,即C /O /O 布料模式(即焦/矿1/矿2 ),此种情况下较前每批上料多 1 批矿石(图 6 ~ 8)。之前上料能力无法满足基本上料,在调整后满足了生产工艺要求。
2 结语
原料系统是高炉炉况稳定的基础,现阶段节能、降低燃料比是大型高炉一直追求的目标,而高炉的上料能力直接影响到高炉的稳定顺行及燃料消耗。合理利用现场设备,调整上料系统的控制程序、排料及布料方式、增加新的料制程序等措施。在不增加成本情况下,提升高炉上料能力,并在异常状态下为生产提供新的调整手段。直接降低燃料比,避免热量流失,为高炉稳定顺行提供保障。