孙利军1 张 晨2 李永昶3
(1. 陕钢集团汉中钢铁有限责任公司炼铁厂设备管理科 陕西勉县 724200;2. 中钢集团工程设计研究院有限公司 北京 100080;3. 陕钢集团汉中钢铁有限责任公司炼铁厂 陕西勉县 724200)
摘 要:以冶金粉尘为原料,在实验室模拟转底炉焙烧制度生产预还原球团,进行产品的物理性能和冶金性能检测,以期满足高炉使用。实验结果表明:预还原球团具有良好的冶金性能,无低温还原粉化﹑无高温还原膨胀﹑软熔性能优良。但是其物理性能差,抗压强度仅有800N,影响高炉块状带透气性,是其大量使用的制约条件。根据物料平衡计算,预还原球团在炉料中仅占到~5%,总体而言利大于弊,可以作为高炉炉料使用。
关键词:转底炉;预还原球团;抗压强度;冶金性能
1 前 言
随着近几年来钢铁行业的发展,对于入炉原料质量的重视以及固废处理的环保要求,国内各大钢铁企业纷纷在固废处理方面加大投资力度,先后建起多座转底炉处理冶金尘泥。但目前利用冶金粉尘生产出的金属化球团品位无法达到《YB/T4170-2008》规定的标准,由于转底炉工艺得到的产品中包括了粉尘中的脉石,导致产品中的TFe含量低。另一个难点是原料中硫含量绝大部分保留在金属化球团中,过高的硫含量显然不适用于炼钢的要求。
日本、韩国投产运行的转底炉,生产的金属化球团作为高炉炉料使用,见表1。其高炉的含铁原料主要在国际市场上购买,炉料结构均以高碱度烧结矿为主,与我国高炉相同,值得借鉴。本文通过实验使用粉尘生产预还原球团,研究其物理和冶金性能是否满足作为高炉冶炼使用,既可以解决冶金粉尘的问题,又能有效利用产物,有着重要的实际意义。
表1 国外转底炉产品利用一览表
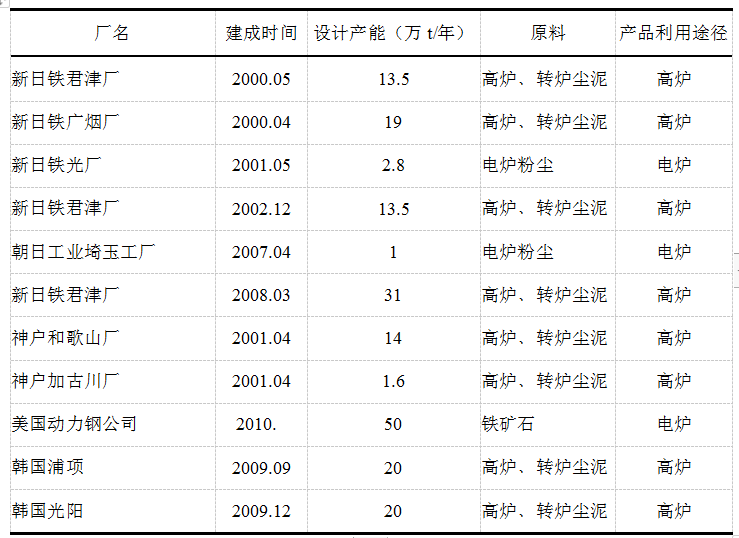
2 实验流程及方法
本次实验所用的粉尘取自江苏S厂和内蒙古B厂,分别标记为S式样和B式样,将各厂不同成分粉尘﹑煤粉﹑粘结剂按比例配料后人工混匀。基于生产实践中粉尘球团金属化率低,焙烧后球团中残碳少情况,提升混合料的C/O达到16.16%。混合好的物料放入圆盘中造球,9~16mm干燥后的圆形球团,取~150g平铺放在刚玉盘上铺两层进行焙烧,焙烧制度:1050-1200℃﹑7min;1200-1300℃﹑10min;1300-1300℃﹑21min,焙烧气氛为氮气气氛。焙烧结束后,每组球团分成两部分,一半进行水淬(强制冷却),一半部分空冷(自然冷却),水淬后的球团需要干燥后称重。首先考察球团金属化率,Zn、Pb、K、Na、S、P脱除率;在满足入炉成分标准《GB/50427-2015》后再进行强度﹑高温爆裂和荷重软化性能性能测试。
3 实验结果与分析
3.1 预还原球团成分
转底炉生产的预还原球团成分取决于冶金粉尘和还原剂的成分,而冶金粉尘的成分与钢铁厂所使用的含铁原燃料有关。两组实验所生产的预还原球团金属化率均大于80%,表3为S厂试样,其化学成分满足高炉冶炼的要求。表4﹑5为B厂式样,可以看出干球成分中K﹑Na含量很高,还原后球团中含量仍很高,达不到入炉标准。转底炉工艺的主要用途为处理含锌含铁冶金尘泥,对铅﹑锌的脱除率很高,但是对于钾脱除率只有50%,钠的脱除率仅30%左右。使用碱金属高的矿石冶炼时,碱金属不仅在粉尘中含量高,在制备的预还原球团中仍很高,这样的球团不易添加进高炉,但仍可作炼钢用。
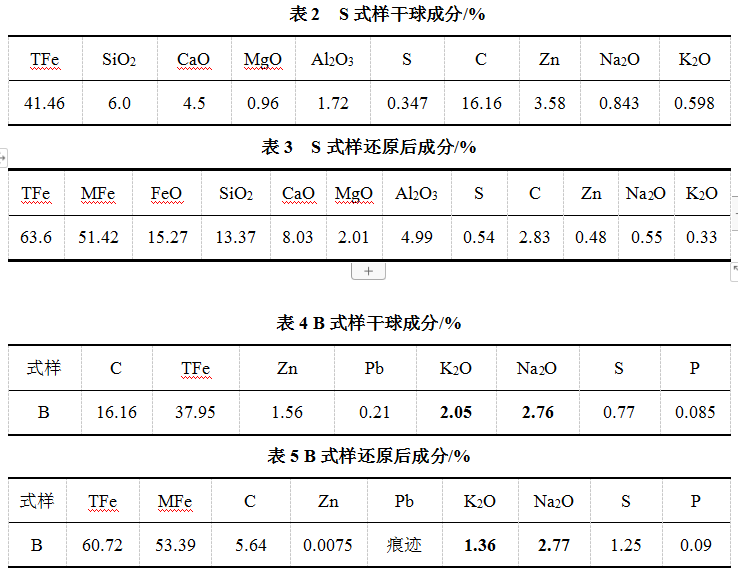
3.2 冷却制度预对预还原球团落下强度的影响
从焙烧后球团强度结果来看,水淬后的球团强度稍差,空冷球团有着很高的强度,落下次数均达10以上,完全能满足实际生产中倒运的要求。因此在预还原球团的冷却工艺设计时,应根据工业应用实际情况,为了避免空冷造成预还原球团表层二次氧化,适当的考虑采用间接冷却工艺,不仅有利于球团提高落下强度,更是对改善作业环境有很大的帮助。
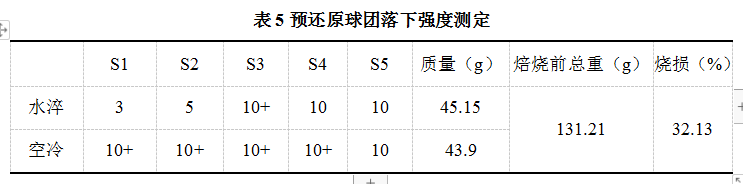
3.3 焙烧制度对成品球抗压强度的影响
从表6可以看出还原焙烧温度从1050—1250℃,球团抗压强度随着金属化率升高而迅速升高;从1250℃提升到1300℃,球团的金属化率变化缓慢,这是由于产生了密实的金属壳层,覆盖在未还原的矿物周围,影响了还原气体的扩散,球团抗压强度变化也随之缓慢。
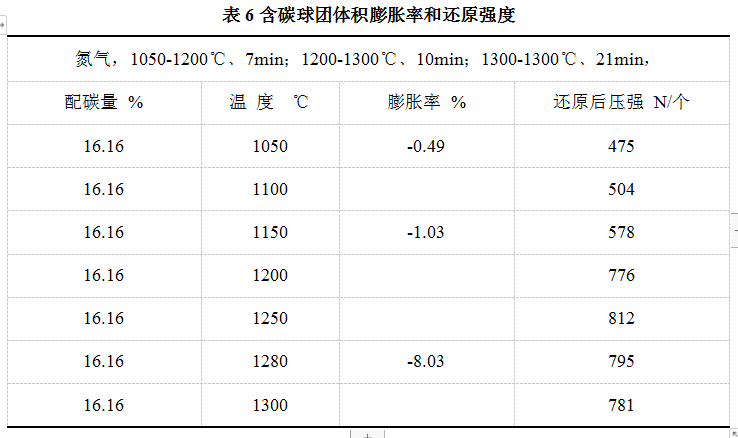
如图1所示,还原时间在从0—30min,球团金属化率逐渐升高,球团强度也升高,30—40min时,变化开始变缓。当还原时间超过40min之后,球团强度会随着金属化率下降而降低。这是因为随着焙烧时间的延长,还原剂消耗量和烧损越来越大,球团内不再排出可燃气体,CO/CO2浓度比下降,还原性气氛消失,部分金属铁又重新被氧化。
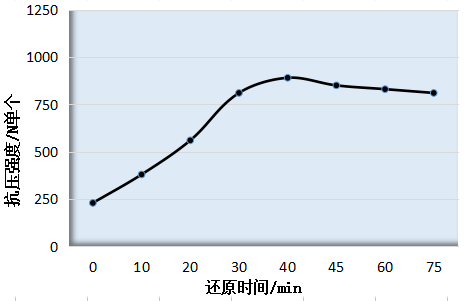
图1预还原球团强度与还原时间关系
综合分析,一方面磁铁矿在中性或还原性气氛下焙烧,当温度超过900℃时,Fe304颗粒被保留下来发生再结晶与晶粒长大,使颗粒互相连接起来。试验研究表明,Fe304再结晶的形式固结的球团矿强度低于Fe203 再结晶的球团矿强度[1]。如图2所示,转底炉还原区气氛为弱还原性。另一方面,随着还原过程的进行,金属铁逐渐被还原出来,球团收缩,颗粒之间连接成致密的整体,使得强度升高。尽管如此,金属铁也只占50%,其抗压强度最大800N,不仅小于Midrex工艺生产的金属化球团强度(图3),也远低于普通氧化球团的抗压强度。
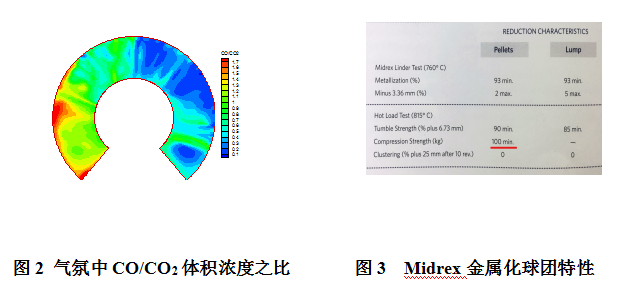
3.4 预还原球团冶金性能指标
图4为预还原球团外貌,转底炉工况下(弱还原气氛﹑微负压),球团整体焙烧状态较好,还原后基本成球,无高温爆裂现象,低熔点共熔现象很少,球团没有发生软熔、粘结的现象,冷却干燥后观察有轻微粉化和结壳情况。由于预还原球团矿是已被部分或大部分还原为直接还原铁,已不属于铁矿石。与氧化球团相比,预还原球团可视为金属附加物。预还原球团在生产过程中已经历过还原,再次加入高炉内,不存在低温还原粉化和热膨胀率的问题。
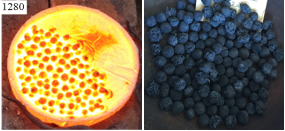
球团内剩余部分未还原的铁和渣,渣中FeO﹑SiO2等生成少量低熔点的渣相。由表7可见,预还原球团开始软化温度约1150℃左右,终了温度约1300℃,软还温度区间窄。综上所述,预还原球团的高温还原膨胀和低温还原粉化性特别好,其软化开始温度相对高,软化区间也相对较窄,具有优良的冶金性能。
4 炉料结构变化对高炉冶炼的影响
近些年来高炉工艺有了很大的提升和改变,但在炉料结构方面,几乎没有变化,仍是由烧结矿﹑球团矿﹑块矿组成。使用预还原球团作为炉料,提高入炉料品位,减少了高炉中对铁矿石氧化还原的负担,从而降低高炉焦比。
I G Tovarovskiy等人甚至考虑从炉顶布料、煤气流分布、软熔带等高炉冶炼过程参数的变化中,找出炉料不同金属化率对焦比的影响[2]。当炉料金属化率小于20%时,降低焦比最多。苏联奥尔斯克钢铁厂在高炉使用金属化球团矿试生产,炉料的金属化率提高到9.6%,高炉生产率提高2.3%,焦比下降5.7%。欧洲设计建造了一座年产160万t的HYL直接还原厂,在传统BF-BOF流程中加入直接还原铁,降低焦炭消耗,减少CO2排放。Midrex直接还原生产HBI,在其高炉中使用,可显著提高铁水产量并降低焦炭消耗,HBI热压铁块的用量最多可达到高炉装载量的30%。
与上述几种工艺生产的金属原料不同,转底炉生产的预还原球团虽然冶金性能优良,但其物理性能较差。作为高炉炉料有利有弊,应积极采取应对措施。加入预还原球团后,烧结矿比例相对减少,球团比例相对增加。一座千万吨级的钢铁厂每年所产生的含铁粉尘约100万t,可生产约78万t预还原球团,全部作为高炉炉料时,占比为4.5%左右。高炉球团矿比例增加后,块状带炉料粒度差别值减小,炉料孔隙度下降,煤气流的阻力损失上升[3]。根据高炉取样表明,炉内低温区氧化球团矿还原后,仍保持结构的完整,其指标要优于烧结矿。而烧结矿在高炉上部的低温区还原时粉化,会使料柱中小于5mm粒级增加,透气性下降,煤气利用率下降。再加入预还原球团,会进一步恶化高炉上部的透气性。‚而在高温区,球团矿高温还原后,强度下降以及膨胀粉化,对高炉高温区透气性产生不利影响,甚至影响软熔带透气性。目前对还原抗压强度尚无一致的标准,日本要求球团矿的还原膨胀率小于20%,还原后的单球抗压强度大于250N[4]。而预还原球团不存在高温膨胀粉化,在高温区仍保持很高的抗压强度,这对高炉冶炼显然是有利的。同时,预还原球团软熔性能优良,有着较高的软化开始温度和较窄的软化区间,保持原炉料结构不变,加入预还原球团后对综合炉料而言,并不会造成软化区间变宽。所以,使用预还原球团的弊端是对块状带的不利影响。
根据宝钢高炉静压力分布,高炉块状带压力阻损占整个高炉压力阻损15%左右,而软熔带和滴落带阻损占到60%左右[5],因此炉料低温还原粉化﹑热爆裂﹑抗压强度低等对高炉影响较小,而炉料高温性能以及球团还原膨胀影响较大。总体而言高炉使用预还原球团利大于弊。
5 结语
利用冶金尘泥生产预还原球团,作为在高炉炉料占比不到5%,自产自销。还具有品位高﹑金属化率高﹑含碳量高等特点,可以提高炉料金属化率,降低焦比。当冶金粉尘中碱金属含量过高时,其脱除率较低,预还原球团中碱金属含量仍很高,不易作为高炉炉料使用。
‚预还原球团具有良好的冶金性能,无低温还原粉化﹑无高温还原膨胀﹑软熔性能优良,有利于改善综合炉料的冶金性能,但其抗压性能最大仅有800N,对高炉块状带不利影响是限制其使用的最大因素。可以通过适当提高烧结矿碱度,提高烧结矿质量,减少低温还原粉化,强化块状带炉料透气性,以抵消预还原球团带来的负面影响。
参考文献
[1] 王筱留. 钢铁冶金学(炼铁部分)[M]. 第3版. 北京:冶金工业出版社,2013:63.
[2] I G Tovarovskiy, Y M Gordon , A E Merkulov. 炉料金属化率对高炉工艺和操作参数的影响[J]. 世界钢铁. 2013,13(5):1-7.
[3] 唐顺兵﹑李夯为﹑梁建华等. 太钢5号高炉高比例球团矿生产实践[J]. 炼铁. 2014,33(5):30-33.
[4] 项中庸﹑王筱留等高炉设计-炼铁工艺设计理论与实践[M]. 第2版. 北京:冶金工业出版社,2014:98.
[5] 朱仁良等. 宝钢大型高炉操作与管理[M]. 第1版. 北京:冶金工业出版社,2015:184.