吴龙 郝以党 吴跃东
(1.中冶建筑研究总院有限公司 北京 100088;
2.中冶节能环保有限责任公司 北京 100088)
摘 要:我国钢渣产生量大,环保要求日益严格,钢渣的洁净化处理及资源利用日益迫切。本文介绍了钢渣辊压破碎余热有压热闷技术的工艺路线和配套专用装备,并进行了有压热闷蒸汽余热发电中试试验,对钢渣余热利用进行了工艺探索,实现了钢渣余热回收的突破。钢渣辊压破碎余热有压热闷技术装备自动化水平高,钢渣处理效果好,是一种新型绿色环保的现代紧凑流程渣处理方式,具有清洁化、装备化、资源化、钢渣不落地、占地面积小等特点,将钢渣处理由工程机械作业方式提升为装备化、自动化作业,为钢渣的环保处理提供了条件,应大力推广应用。
关键词:钢渣;资源利用;热闷
1 前言
钢渣是伴生炼钢过程产生的固体废弃物,每冶炼一吨约产生12~15%的钢渣。2018年我国钢渣总产生量约1.2亿吨,钢渣产生量十分巨大。钢渣主要成分由硅酸钙类矿物、金属铁和铁氧化物等化学物质组成。硅酸钙类矿物及其他成分主要由硅酸二钙(2CaO·SiO2)、硅酸三钙(3CaO·SiO2)、橄榄石(CaO·RO·SiO2)、蔷薇辉石(3CaO·RO·2SiO2)以及RO相(MgO、MnO、FeO的固溶体)等组成。
目前钢渣主要作为建筑材料和道路用料,但由于钢渣中含有一定的游离钙镁氧化物,钙镁氧化物遇水膨胀,带来了钢渣作为建筑等材料的安性性问题,致使大量的钢渣无法有效利用。2019年,我国钢渣实际利用率不到30%,钢渣资源浪费,占用大量土地,并可能污染环境,迫切需要合理的处理方式和消化途径。近年来我国环境排放标准日益提高,钢渣的资源化和环境排放要求的提高对钢渣处理利用技术也提出了更高的要求。本文对钢渣处理技术的发展进行了阐述,详细介绍了钢渣辊压破碎余热有压热闷工艺及开发历程,并针对钢渣辊压破碎余热有压热闷理术的应用实践进行了阐述。
2 钢渣热闷原理和技术发展
2.1 钢渣热闷原理
炼钢过程添加大量石灰,由于造渣时间较短,过量的CaO、MgO还未能完全熔化,以游离态在钢渣中包裹。钢渣热闷处理是在密闭容器内利用钢渣余热,对热态钢渣进行打水产生过饱和水蒸气,促进钢渣中f-CaO和水蒸气快速反应消解。热闷过程中发生复杂的物理和化学作用,具体特点如下:
(1)钢渣急冷破裂。高温钢渣遇到大量水产生急剧温降,熔渣快速冷却过程中各矿物发生剧烈的相变,产生应力使钢渣破裂。
(2)汽蒸作用。高温渣和热闷打水反应产生大量温度在105℃以上、且具有一定压力的过饱和水蒸汽。这种环境促进了水蒸汽向破裂的钢渣缝隙内扩散、渗透,有利于f-CaO消解反应的进行。
(3)硅酸二钙(C2S)晶型转变。在钢渣从750℃冷却到650℃过程中,硅酸二钙(C2S)由β- C2S转变为γ- C2S,体积膨胀10%,钢渣继续碎裂。
(4)钢渣和过饱和水蒸气封闭条件下f-CaO与水反应生成Ca(OH)2,体积膨胀98%,f-MgO与水反应生成Mg(OH)2,体积膨胀98%。
钢渣热闷即基于上述的物理化学作用破碎、粉化,消除了钢渣不稳定性,促进了渣铁分离。钢渣热闷过程发生的主要反应为游离氧化钙和游离氧化镁的反应。钢渣中f-CaO因过烧而结晶致密,活性差,常温下水化反应慢,自然条件下往往需要数年的时间才能全部消解。水蒸气浓度含量越大,压力越高越有利于f-CaO的消解反应,且在反应能够进行的条件下温度越高反应速率也较快。
2.2 钢渣热闷技术的发展
为解决钢渣快速破碎和安定性问题,中冶建筑研究总院与有关单位于1992年研究成功第一代钢渣热闷处理技术,是将钢渣热泼,落地冷却到400℃左右再铲运倾倒在热闷装置内,盖上盖密封喷水产生蒸汽,和钢渣发生物理力学和化学反应而开裂粉化。但存在钢渣热泼落地环境污染、占地面积大、处理时间长等缺点。
2004年成功开发第二代钢渣热闷处理技术。为了缩短钢渣处理周期,将液态钢渣热泼落地,冷却到800℃时用铲车或抓斗机将钢渣运往热闷装置倾翻,然后盖上盖密封喷水热闷。第一代热闷装置内衬钢板在800℃易变形,第二代工艺采用耐热铸铁板作内衬。存在的问题是没有彻底解决钢渣热泼落地环境污染、占地大的问题,并存在800℃钢渣损坏抓运设备的问题。
2008年成功第三代熔融钢渣热闷处理技术,是将1650℃左右的钢渣直接倾翻在热闷装置内,喷水使其表面固化,然后盖上装置盖间断喷水,直到钢渣温度降到65℃左右时热闷结束。该技术基本解决了以往的占地和环保排放问题,但仍存在装备自动化水平不够高、热闷周期仍较长的问题。
2012年成功研发第四代钢渣热闷处理技术即熔融钢渣辊压破碎—余热有压热闷新技术。先后进行实验室模拟实验和中试试验后,并最终在河南省济源钢铁(集团)有限公司建设了示范生产线,实现了工业化生产,在热闷技术装备和自动化水平实现了巨大的进步。
3 钢渣辊压破碎-余热有压热闷新技术
围绕有压热闷工艺,中冶建筑研究总院研发了系统的工艺装备技术,其中核心装备主要有钢渣辊压破碎装置和有压热闷罐,具体如图1所示。
图1钢渣有压热闷主要装备
熔融钢渣高效罐式有压热闷处理技术大致可分为钢渣辊压破碎和余热有压热闷两个阶段。辊压破碎阶段主要是完成熔融钢渣的快速冷却、破碎,此阶段的处理时间约30min,经过此阶段的处理,可将熔融钢渣的温度由1600℃左右冷却至600℃左右,粒度破碎至300mm以下。余热有压热闷阶段主要是完成经辊压破碎后钢渣的稳定化处理,此阶段的处理时间1.5-3h,处理后钢渣的稳定性良好,其游离氧化钙含量小于2.5%,浸水膨胀率小于1.5%。
钢渣余热有压热闷技术配套自主研发的关键工艺装备主要有:渣罐倾翻车、辊压破碎机、渣槽转运台车和钢渣有压热闷装置。此种钢渣处理新工艺与目前使用比较广泛的钢渣池式热闷工艺相比较,满足现代炼钢钢渣处理高效化、装备化、安全清洁化生产要求,使得钢渣处理过程更加清洁高效,改善了现有钢渣稳定化处理工艺操作环境差,工人劳动强度大和处理周期长等不足。
钢渣辊压破碎-余热有压热闷技术与现有常压池式热闷技术相比,具有以下几个独特优势:
(1)热闷周期短,约2h,处理效率高,与普通现有常压池式热闷工艺相比缩短7-10h;
(2)自动化水平高,工作定员人数少;
(3)处理过程洁净化程度高,作业环境好,环保水平高;
(4)热闷后的钢渣粉化率高,粒度小于20mm的钢渣含量大于70%,浸水膨胀率小于2%,稳定性好;
(5)钢渣处理生产过程烟气排放浓度<10mg/Nm3,满足超净排放要求。
(6)建设成本和运营成本低,运营成本可节约40%。
有压热闷罐处理是全密闭体状态下进行的,相比以往钢渣处理技术洁净化程度更高,更加环保;此外,有压热闷罐处理过程在封闭罐体内产生大量蒸汽,可望进行整合发电,为钢渣显热的回收利用创造了条件。
4 有压热闷余热发电探索试验
在科技部环保院所技术开发研究专项经费的支持下,自2012年针对钢渣余热回收技术进行研究。有压热闷工艺为钢渣余热回收发电提供了连续、有压、可控的高温蒸汽,具备进行发电回收钢渣余热的物质条件基础。
2015年起,项目研发团队在沧州中铁进行有压热闷发电中试试验的准备工作,于2016年初完成中试试验线建设。本发电热源来源于沧州中铁钢铁公司钢渣处理车间热闷反应罐产生的有压蒸汽,蒸汽管道共接自两个热闷罐,经由蒸汽主管道送至汽水热交换器进行换热。
钢渣余热有压热闷蒸汽温度120℃,压力0.2-0.4MPa,采用有压热闷蒸汽经换热器加热其中的密闭循环水,加热后的循环水进而加热发电工质,最终通过工质驱动发电机发电。图2为有压热闷余热发电中试试验现场。
图2钢渣有压热闷余热发电中试现场
2016年钢渣有压热闷余热发电中试试验结果表明,该试验线运行稳定,可靠,通过整合有压热闷蒸汽可进行发电;通过该方式进行钢渣余热发电可望实现吨钢渣发电量3~5kWh,未来可进行更大规模的发电工业试验,实现钢渣余热的回收利用。
5 工业生产推广应用
钢渣辊压破碎余热有压热闷处理工艺技术在经过一系列系统化研究和工业优化设计后,已成功应用于国内首钢京唐钢铁有限公司、江苏镔鑫钢铁有限公司等26家钢铁企业,并出口至“一带一路”沿线马来西亚联合钢铁集团,累计建设钢渣处理生产线54套,合同金额23.54亿元。
2012年10月,河南济源钢厂完成了首套产业化示范推广应用工程。现已投产运行超过8年,生产经验表明,采用该技术钢渣处理效果良好,实现处理后的钢渣中-20mm粒级超过75%,游离氧化钙含量小于2.5%,浸水膨胀率小于1.5%,尾渣中金属铁小于1.5%。
图3 河南济源钢铁60万吨/年钢渣处理生产线现场
2017年由中冶节能环保有限责任公司EPC总承包的江苏镔鑫钢铁集团70万吨/年钢渣有压热闷处理及加工提纯生产线工程一次带料成功,顺利投产,该项目首次采用钢渣立式有压热闷技术。钢渣立式有压热闷技术是中冶节能环保有限责任公司在卧式有压热闷技术的基础上,对工艺流程重新进行优化,取消装渣车运转与轨道对接等工序,大多缩短了原有工艺流程。该技术在未经过任何工业试验的基础上直接在实际过程中应用,运行效果取得了业主的认可与好评。
2019年5月,首钢京唐钢铁有限公司设计能力60万吨/年钢渣处理生产线正式投产。系统装备运行稳定可靠,钢渣处理效果良好。项目针对钢渣生产过程烟气治理实施湿式电除尘器湿法除尘技术,实现了钢渣处理过程烟气排放浓度稳定达到<10mg/Nm³的超低排放效果。项目是本技术及装备成功首次应用于国内一流钢铁企业,有力的推动国内钢渣处理利用项目开拓。
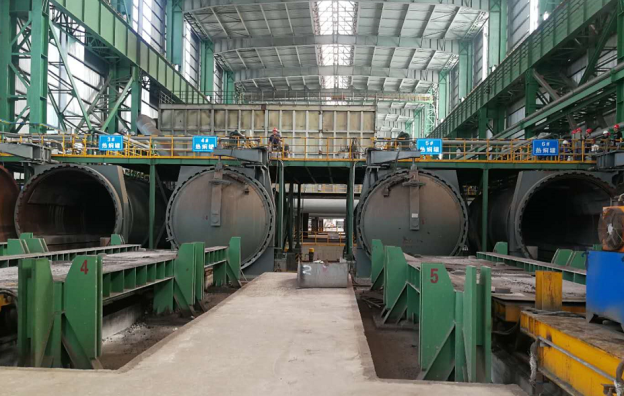
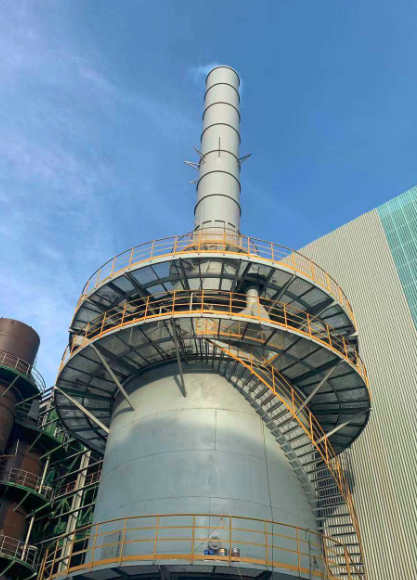
图4 首钢京唐60万吨/年钢渣处理生产线现场
联合钢铁(大马)集团钢渣处理生产线设计能力50万吨/年,该生产线于2018年6月正式投产,现已投产运行2年多。系统装备运行稳定可靠,钢渣处理效果良好。项目针对钢渣生产过程烟气治理实施湿式电除尘器湿法除尘技术,实现了钢渣处理过程烟气排放浓度稳定达到<10mg/Nm³的超低排放效果。项目是本技术及装备成功出口至“一带一路”沿线马来西亚,为钢渣处理技术的国际市场应用建立了典型示范。
图5 联合钢铁(大马)集团60万吨/年钢渣处理生产线现场
6 结语
近年来,我国工业发展迅速,环境问题也日益严重,钢渣的资源化利用也日益紧迫。以钢渣辊压破碎-余热有压热闷技术为代表的钢渣预处理技术具备更高的装备化、自动化水平,可实现钢渣处理的高效化、连续化生产,钢渣处理效果好,系统装备占地少,配套土建、公辅投资低。新技术在钢渣处理具有更为显著的技术优势以及极具竞争力的价格优势。此外,本技术应用过程更加环保等优点,能够满足我国日益提高的环境排放标准,符合装备化自动化提升需求,是未来钢渣处理技术应用的可靠选择。目前国内50%以上的钢渣处理仍采用落后的热泼生产工艺,当前形势下钢铁企业应提高钢渣处理的技术水平和装备水平,以满足日益严格的环保要求。加快淘汰钢渣热泼等落后的处理方式,大力推广钢渣辊压破碎余热有压热闷技术技术,早日实现钢渣的清洁化、高效化、装备化处理。