李佳俊
(玉溪新兴钢铁有限公司)
摘要:玉钢两座450 m3高炉于2008年开始实施钒钛矿冶炼,炉渣TiO2含量达到11.5~14.0 %,属于典型的“中钛渣”。 玉钢炉渣性能在很大程度上受渣中TiO2还原程度的影响,其熔化性温度较高、熔化性温度区间较窄,在正常炉况下液态炉渣的粘度约0.5Pa.S,能满足高炉强化冶炼的要求。本文旨在通过对高炉冶炼钒钛矿的炉渣特性进行分析研究,找出适宜的炉渣组成结构,并提出高炉合理造渣制度的控制要求。
关键词: 钒钛矿冶炼;渣相结构;炉渣粘度;熔化性粘度
玉钢1、2号高炉于2005年 2月建成投产,高炉设计炉容为450 m3,风口数目为14个,进风面积0.144 m2。2008年因原料供应紧张,高炉维持均衡稳定经济生产受到威胁,玉钢公司经过充分调研之后,决定组织开展钒钛矿冶炼和提钒炼钢的生产工艺技术路线转型。玉钢公司于2008年5月在完成了球团矿筛、水冲渣系统、炉前出铁场4#铁沟,旋风除尘及新建4#热风炉等一系列的重大改造之后,决定正式组织实施高炉钒钛矿冶炼的工业性试验。钒钛矿冶炼的难点在于控制好渣铁流动性,使冶炼进程能够正常进行。根据炉渣的物理化学特性,进入渣中的TiO2会形成碳氮化钛、镁铝尖晶石、富钛透辉石、攀钛透辉石等物相,这些物相的熔点相差很大,如炉渣中熔点最高的碳氮化钛熔点约为3 000 ℃左右,而熔点最低的攀钛透辉石熔点仅为1 200~1 300 ℃,两者相差1 700~1 800 ℃。炉渣中相关物相的化学成分、组织结构及含量的变化,都会导致炉渣熔点、粘度等性能的变化,从而对高炉冶炼行程造成影响。所以研究炉渣的组成结构对钒钛矿冶炼的意义重大,本文旨在通过对高炉冶炼钒钛矿的炉渣特性进行分析研究,找出合理的炉渣组成结构,并提出高炉合理造渣制度的控制要求。
1 高炉炉料结构及炉渣成分比对
1.1 玉钢高炉炉料结构及原料成分
玉钢实施钒钛矿冶炼期间典型的炉料结构及原燃料成分详见表1~表4。
表1 炉料结构
焦炭批重 |
矿石批重 |
烧结矿 |
钒钛球团 |
3.7 t/批 |
14.0 t/批 |
70 % |
30 % |
表2 烧结矿成份分析
TFe /% |
CaO/% |
SiO2/% |
FeO/% |
MgO/% |
AL2O3/% |
TiO2/% |
V2O5/% |
R2 |
S/% |
51.30 |
12.80 |
6.58 |
7.16 |
2.78 |
1.453 |
2.540 |
0.224 |
1.94 |
0.051 |
表3 钒钛球团矿成份分析(%)
TFe |
CaO |
SiO2 |
MgO |
S |
AL2O3 |
TiO2 |
V2O5 |
MnO |
54.24 |
0.90 |
4.56 |
1.39 |
0.005 |
1.58 |
11.396 |
0.719 |
0.19 |
表4 焦炭成份(%)
H2O |
A |
V |
C |
S |
4.63 |
15.26 |
1.08 |
83.26 |
0.52 |
从表1~4中可以看出,玉钢实施钒钛矿冶炼期间,典型的炉料结构为“70 %烧结矿+30 %钒钛球团矿”,其中烧结矿含TiO22.54 %,钒钛球团矿含TiO211.40 %、含V2O5 0.72 %。
1.2 钒钛矿冶炼炉渣成分比对
云南及周边相关钢厂实施钒钛矿冶炼的炉渣成份比对见表5。
表5 各钢厂钒钛矿冶炼炉渣成分
|
SiO2% |
CaO/% |
AI2O3/% |
MgO/% |
S/% |
FeO/% |
TiO2/% |
R2 |
川威 |
24.91 |
31.98 |
13.62 |
8.59 |
1.00 |
/ |
15.98 |
1.28 |
24.11 |
32.36 |
11.63 |
8.53 |
0.29 |
/ |
17.98 |
1.34 |
|
德钢 |
26.83 |
33.6 |
/ |
8.67 |
/ |
0.95 |
/ |
1.25 |
26.49 |
33.38 |
14.04 |
8.9 |
0.996 |
0.88 |
13.33 |
1.26 |
|
26.99 |
32.89 |
14.72 |
8.52 |
0.964 |
1.07 |
12.74 |
1.22 |
|
新钢业 |
24.80 |
27.41 |
/ |
/ |
/ |
/ |
21.38 |
1.105 |
24.71 |
27.39 |
/ |
/ |
/ |
/ |
21.49 |
1.108 |
|
24.39 |
27.03 |
/ |
/ |
/ |
/ |
21.95 |
1.090 |
|
攀钢 |
24.64 |
27.05 |
14.15 |
7.56 |
0.456 |
/ |
22.19 |
1.10 |
24.48 |
26.88 |
14.41 |
7.89 |
0.456 |
/ |
22.46 |
1.10 |
|
24.33 |
27.37 |
14.36 |
8.12 |
0.502 |
/ |
22.63 |
1.12 |
|
玉钢 |
29.85 |
32.52 |
11.52 |
6.93 |
0.459 |
1.12 |
12.429 |
1.09 |
29.99 |
32.63 |
11.67 |
6.93 |
0.436 |
0.89 |
14.010 |
1.09 |
|
34.25 |
37.71 |
12.30 |
6.89 |
0.389 |
1.09 |
11.505 |
1.10 |
从表5中可以看出,与周边几家同样实施钒钛矿冶炼的厂家相比,玉钢高炉渣成份具有如下特点:1)炉渣碱度及渣中MgO含量相对较低,分别为1.10倍左右和6.8 %左右;2)渣中TiO2含量也相对较低,有11.5~14.0 %,属于中钛渣水平,与德钢渣TiO2含量接近,仅有攀钢渣中钛含量的60 %存在;3)渣中FeO含量为0.89~1.12 %,与德渣中FeO含量接近,表明玉钢高炉渣中带铁控制情况较好,已与长期坚持钒钛矿冶炼的德钢控制水平基本一致。
2 玉钢高炉渣特性实验研究
为了探索钒钛矿冶炼高炉渣的特性,寻找到适宜的渣相结构和合理的造渣制度,玉钢专门委托昆明理工大学开展了一系列的实验研究工作。
2.1 不同TiO2含量炉渣特性分析
昆明理工大学实验室对玉钢不同TiO2含量条件下,炉渣熔化性温度、物相组成,以及温度-粘度曲线检测结果见表6、表7和图1。
表6 不同TiO2含量炉渣熔化性温度检测结果
不同含钛炉渣的矿物组成 玉钢高炉不同TiO2含量炉渣
表7 不同TiO2含量炉渣物相检测结果(%)
系列1 TiO2—16% 系列2 TiO2—18% 系列3 TiO2—20%
图1 不同TiO2含量炉渣温度-粘度曲线
从表6、表7和图1可以看出,随着渣中TiO2含量增加,炉渣的熔化性温度呈逐步升高的趋势,当渣中TiO2含量超过18 %以后,渣相中钛辉石含量明显增加,炉渣的熔化性温度已经超过程1 400 ℃,这会对炉缸的安全稳定运行造成一定影响,也对高炉工长的操控稳定性提出了更高的要求。
2.2 不同Al2O3含量温度-粘度曲线分析
不同Al2O3含量炉渣温度-粘度曲线见图2。
1—12.5%,2—11% ,3—9%
图2 不同Al2O3含量炉渣温度-粘度曲线
从图2中可以看出,玉钢高炉渣Al2O3含量在9~12.5 %范围内,Al2O3含量变化对炉渣粘度的影响并不大。
2.3 不同的 MgO含量炉渣温度-粘度曲线分析
不同MgO含量炉渣温度-粘度曲线见图3。
1—7.5%; 2—8.0%; 3—8.5%;4—9.0%
图3 不同MgO含量炉渣温度-粘度曲线
从图3中可以看出,随着MgO含量在7.5~9.0 %范围内逐步提高,玉钢炉渣熔化性温度有上升的趋势,因此在玉钢条件下,开展钒钛矿冶炼,渣中MgO含量不宜过高。
2.4 不同碱度炉渣温度-粘度曲线分析
不同碱度炉渣温度-粘度曲线见图4。
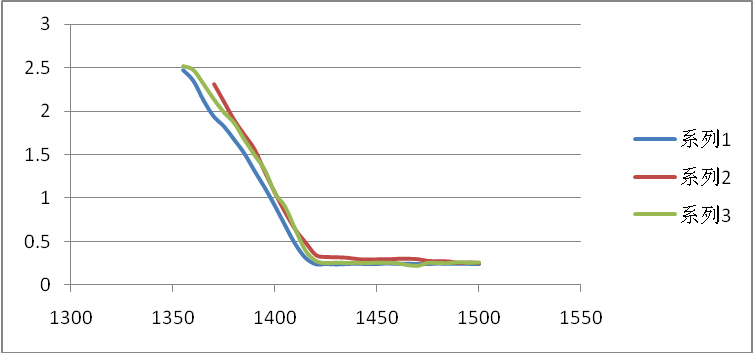
1—R=1.15 2—R=1.20 3—R=1.25
图4 不同碱度炉渣温度-粘度曲线
从图4中可以看出,炉渣碱度对炉渣粘度和熔化性温度影响并不明显,实际生产中可
以根据高炉冶炼需要对炉渣碱度进行相应调整。
3 玉钢高炉渣实际取样检测结果分析
3.1 实际生产中高炉铁水成分及炉渣成分分析
在玉钢冶炼钒钛矿冶炼的实际生产中,典型的铁水成分及炉渣成分见表8。
表8 高炉铁水成分及炉渣成分分析
炉次 |
Si % |
V % |
Ti % |
SiO2 % |
CaO % |
AL2O3 % |
MgO % |
MnO % |
S % |
FeO % |
TiO2 % |
R2 |
1 |
0.26 |
0 .267 |
0.315 |
29.99 |
33.19 |
11.80 |
6.96 |
0.51 |
0.484 |
0.88 |
13.102 |
1.11 |
2 |
0.24 |
0.265 |
0.322 |
30.19 |
33.37 |
11.82 |
6.96 |
0.51 |
0.489 |
0.87 |
12.646 |
1.11 |
3 |
0.24 |
0.281 |
0.285 |
30.20 |
32.96 |
11.88 |
6.97 |
0.52 |
0.485 |
0.83 |
13.118 |
1.09 |
4 |
0.26 |
0.270 |
0.290 |
30.25 |
33.25 |
11.84 |
6.97 |
0.59 |
0.459 |
0.91 |
12.655 |
1.10 |
5 |
0.25 |
0.264 |
0.302 |
29.93 |
31.91 |
11.63 |
6.97 |
0.79 |
0.414 |
1.06 |
12.913 |
1.07 |
6 |
0.25 |
0.288 |
0.295 |
29.85 |
32.52 |
11.52 |
6.93 |
0.58 |
0.459 |
1.12 |
12.429 |
1.09 |
7 |
0.25 |
0.281 |
0.367 |
30.42 |
32.68 |
12.02 |
6.93 |
0.55 |
0.470 |
0.96 |
13.333 |
1.07 |
8 |
0.24 |
0.261 |
0.237 |
29.99 |
32.63 |
11.67 |
6.93 |
0.66 |
0.436 |
0.89 |
14.010 |
1.09 |
从表8中可以看出,在玉钢实际生产过程中,铁水[Si]含量控制较低,稳定性较好,与此相对应,比较适宜的炉渣成份控制范围为TiO2含量12.5~14%,MgO含量6.90~7.0%,Al2O3含量11.5~12%,炉渣碱度R2为1.07~1.11倍。
3.2 高炉渣实际取样温度-粘度曲线检测结果分析
玉钢实施钒钛矿冶炼期间,炉渣温度-粘度关系详见图5
图5 高炉渣实际取样温度-粘度曲线
玉钢高炉渣熔化性温度为1 320~1 360 ℃,与普通高炉渣相比具有熔化性温度高、结晶性能强的特点[1]。随着渣中TiO2含量逐渐降低,渣中钙钛矿、镁铝尖晶石和镁黑钛石等高熔点矿物含量逐渐降低,炉渣熔化性温度逐渐降低;在正常炉缸工作温度下,高炉渣粘度一般为0.5Pa·s左右,能够满足高炉生产的要求。
高炉治炼能够正常进行,首要条件是防止炉渣变稠,根据钒钛矿冶炼研究的结果表明,TiN和TiC在软熔带以上就开始生成,最初生成的TiN和TC是由与铁结合的TiO2优先反应生成的,与金属铁共生。而大部分TiC、N),是在软熔带以下,从滴落带至风口平面,由炉渣中的TiO2生成的,这一区间是Ti(C、N)的关键生成区间。炉渣中的Ti(C、N)含量在风口平面达到最高值,在风口平面以下Ti(C、N)含量逐步减少,到达渣口平面Ti(C、N)含量接近终渣水平[2]。
一般认为,Ti(C、N)通常以几微米的固体悬浮物呈弥散状分布在炉渣中,是导致炉渣变稠的主要原因;炉渣中夹杂的大量表面包裹着T(C、N)微粒不能相互汇聚的铁珠,是炉渣黏度剧增的重要原因[3]。玉钢高炉冶炼钒钛矿期间,高炉炉况稳定顺行,主要技术经济指标不断改善,长期的生产实践证明,玉钢已经掌握了高炉冶炼钒钛矿的关键技术,中钛型钒钛渣的造渣制度不会为高炉强化冶炼的限制性环节。
4 结论
(1)玉钢两座450 m3高炉于2008年开始使用钒钛矿冶炼以来,渣中TiO2含量长期保持在11.5~14.0%之间,与周边德钢高炉渣的TiO2含量接近,属于典型的“中钛渣”。
(2)玉钢高炉渣具有熔化性温度高、结晶能力强,可操作温度区间窄等特点,对高炉的精益操作和管理提出了新的要求,长期的生产实践证明,造渣制度不会成为玉钢实施钒钛矿冶炼的限制性环节。
(3)根据实验研究结果和生产实践经验,作者提出玉钢相对适宜的造渣制度为R2 1.05~1.15倍,TiO2含量11.5~14%,MgO含量6.5~7.5,FeO含量0.85~1.10%。
参考文献
[1] 丁跃华,钒钛矿高炉冶炼技术.技术总结
[2] 王莜留,高炉生产知识问答[M].北京:冶金工业出版社,2004.
[3] 周传典,高炉炼铁生产技术手册[M].北京:冶金工业出版社,2003.