多工艺协同降低烧结机工序能耗生产实践
李国良,李乾坤,周晓冬,李秭城,裴元东
(中天钢铁集团有限公司 第二烧结厂,江苏 常州 213000)
摘要:针对烧结工序能耗高,而一种工艺的改善或新工艺的推出对其工序能耗的改善有限,本文从低水低碳厚料层烧结、低热值煤气低负压点火、料面喷吹天然气等多工艺协同处理出发,结合漏风治理、增设边缘压料装置优化烧结料面布料等生产控制措施,在改善烧结矿产、质量的同时,取得了降低工序能耗的良好效果,烧结工序能耗由 53.66 kgce/t-s 逐步降低到 46.32 kgce/t-s。
关键词:协同;工序能耗;厚料层;低负压;天然气喷吹
当前国内钢铁产能日趋饱和,原燃料价格上涨明显,给钢铁行业发展带来了很大的挑战,节能降耗逐渐成为钢铁行业发展的必由之路。我国钢铁行业能耗占整个国民经济的14%以上,其中烧结工序能耗占整个钢铁行业能耗的 10%以上[1-2],因此,降低烧结工序能耗意义重大。
针对降低烧结工序能耗前人开展了众多生产研究实践,主要从改善烧结原燃料结构、提升混合料温、热风烧结、漏风治理、控制燃料破碎粒度、厚料层烧结工艺制度等方法进行了实践探究,取得了较好的效果[2-4]。但是常规工艺和单一新工艺的改进对降低烧结工序能耗的效果有限。为更好地解决此问题,本文以中天钢铁 550 m2烧结机工艺为基础,从低水低碳厚料层烧结、低热值煤气低负压点火、料面喷吹天然气等多工艺协同处理出发,结合漏风治理、增设边缘压料装置优化烧结料面布料等生产控制措施,试图在改善烧结矿产、质量的同时,取得降低工序能耗的良好效果,为同类工程提供借鉴与参考。
1 降低工序能耗生产工艺
1.1 低水低碳厚料层烧结工艺
厚料层烧结是降低燃料消耗的重要手段。宝钢、马钢、首钢京唐、泰钢、天钢、湘钢等企业烧结料厚已达 900~1 000 mm 水平。本文涉及的烧结机台车栏板改造前高度为 750mm,设计料层厚度为 700~750 mm,为充分利用厚料层烧结自动蓄热特点,将点火炉抬高,逐步将料层厚度由 800 mm 抬高至 920 mm 水平,超烧结机台车栏板高度 170 mm(见图 1)。 随着料层厚度的提升,烧结机机速放慢,烧结料的高温保持时间增加,液相生成更加充足,烧结矿的转鼓强度由 77%提升至 78%。为减少过湿层和燃烧层对厚料层烧结透气性的影响,在实施厚料层后重点采取了低水烧结措施和燃料粒度优化控制:①采取一混多加水、二混少加水;②加装雾化喷头保证原料制粒成球效果;③为消除混合矿槽蒸汽预热不均的问题,采用了蒸汽管道输堵装置;④采用熟熔剂烧结,充分利用生石灰消化放热提升混匀料料温。在各项措施实施后,混合料水分从 7.5%降低到 6.8%,混合料料温提高到 70℃水平;⑤优化燃料粒度控制,用锤破替代对辊,在增强破碎能力的同时减少四辊负荷,实施后燃料粒度控制在小于 0.5 mm 占比为 20%,0.5~3 mm 占比为 75%,大于 5 mm占比为 8%的综合水平。由于厚料层烧结过程自动蓄热作用的发挥[2],固体燃料配比由4.6%降低到 4.3%,降低 0.3%,折合吨矿固体燃耗下降 3.75 kg/t-s[5]。
1.2 低热值煤气的低负压点火工艺技术改造
本文烧结生产所用点火气体燃料为高炉煤气、转炉煤气,原前 3 个风箱开度分别为40%、60%、60%,抽风负压分别为-14.25、-14.23、-14.16 kpa。由于负压较高,煤气被大量抽走,降低了煤气的利用率,导致煤气消耗增大,同时也不利于烧结矿产、质量的提升。为改善这种高负压、大风量的点火制度,烧结厂于 2019 年初逐步在烧结机上进行点火炉前移工艺技术改造(见图 2)。结合图 2,当将 1#、2#风箱翻板关闭,3#风箱翻板开度至50%时,1#、2#、3#风箱点火负压由原来的-14 kpa(平均值)分别降低至-8.23 -8.44. -10.22kpa,烧结机点火煤气单耗由 38.15 m3/t 降低至 32.36 m3/t,降低了 5.79 m3/t。厚料层烧结制度推行后,烧结机机速降低,点火时间延长,点火强度得到了提升[2]。同时,由于前部风箱负压降低,更多的风量后移,保证了后续燃烧带的反应,使整个烧结过程进行的更加充分,烧结矿强度得到一定的提升,由 77.89%提升到 78.26%,提升了 0.37%[5]。
图 2 点火炉前移改造方案示意
1.3 料面喷吹天然气工艺技术的应用
日本 JFE 提出了料面喷吹天然气工艺[6-7],国内梅钢、韶钢等企业使用料面喷吹焦炉煤气,均取得较好效果[8]。2020 年,中天在 550m2烧结机上成功实施了国内首台套烧结机料面喷吹天然气工艺和装备。天然气喷吹装置设计量程为 0~600 Nm3/h,天然气喷吹后 550m2烧结机固体燃耗下降明显。在天然气喷吹量为 300 Nm3/h 制度下,烧结机固体燃料(无烟煤)配比下降 0.2%~0.3%,折合吨矿固体燃耗下降 2.9~4.3 kg/t-s。相较于未喷吹天然气烧结矿表层强度提升,内返率降低了 0.3%,转鼓强度由 78.49%提升至 78.77%,提升 0.28%。
同时,现场试验在 550 ㎡烧结机上料量为 1 030 t/h,烧结混匀料堆成分固定,料层厚度为920 mm,烧结机机速为 2.3 m/min,固体燃料洗精煤配比为 4.3%的基准条件下,探究了不同天燃气喷吹量对烧结过程和烧结矿质量的影响,其天然气喷吹装置如图 3 所示,不同喷吹量对烧结终点温度、废气温度、负压的影响如表 1 所示,不同喷吹量对烧结矿质量的影响如表 2 所示。
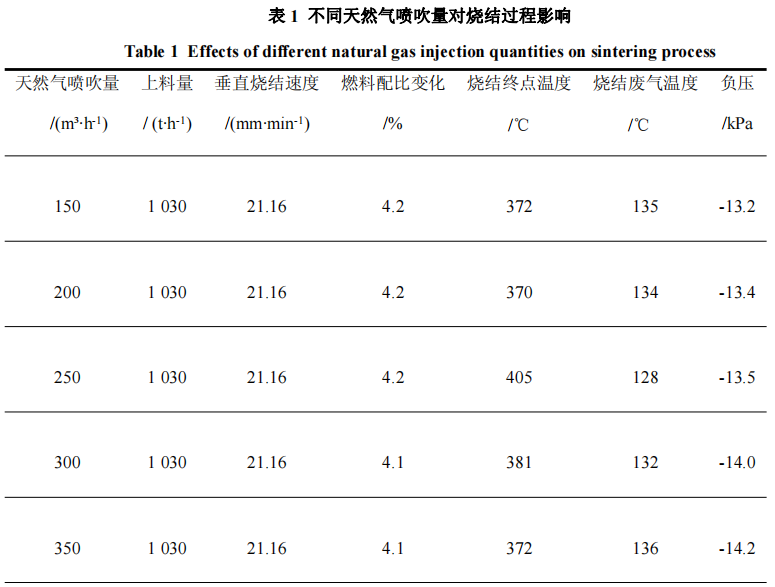

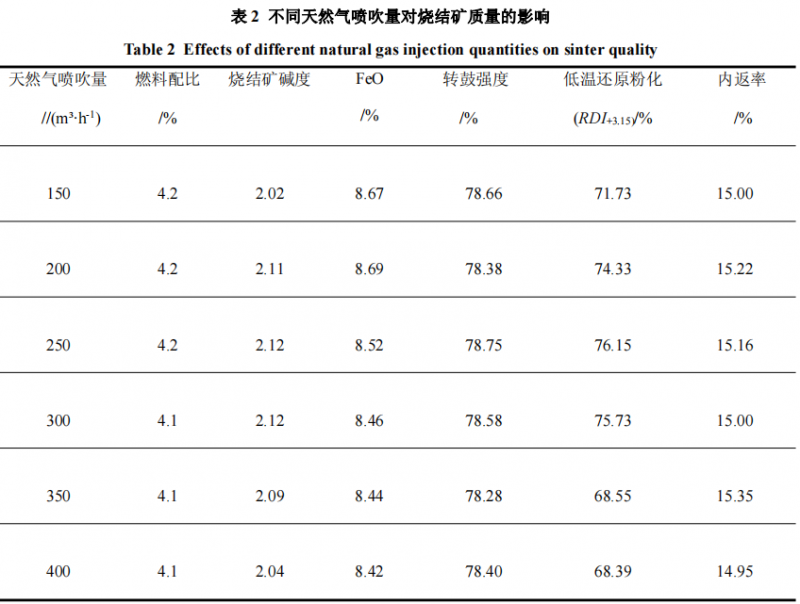

由表 1、2 可知:在烧结料层厚度一定,上料量一定的条件下,随着天然气喷吹流量的加大,固体燃料配比适当降低,烧结终点温度出现先升高后降低的变化趋势,烧结负压呈现逐步增加的趋势;烧结矿 FeO 质量分数降低,转鼓强度呈现波动变化,低温还原粉化性能 RDI+3.15呈现先升高后降低趋势,即在喷吹量超过 300 m3/h 后较基准有所降低。分析原因认为,当烧结料面喷吹天然气过多后,两种燃料(燃气和固体燃料)燃烧出现的燃烧带可能出现不匹配,因而造成高温带透气性变差,烧结负压有所升高。因此,在当前条件下喷吹量过大可能会对烧结过程产生负面影响[9]。
2 降低工序能耗强化措施
为进一步强化厚料层烧结工艺和料面天然气喷吹新工艺对降低工序能耗的效果,现场进一步采取了漏风治理、优化烧结料面布料等生产控制措施。
2.1 漏风治理
烧结机的漏风是行业的共性问题,降低漏风对于改善烧结产、质量和降低主抽风机电耗有利,从而可降低烧结工序能耗。烧结机主要漏风点包括台车栏板错位部分、台车栏板插销处、烧结机台车弹性滑道与固定滑道间油封处、风箱大烟道内壁磨损严重处、大烟道双层卸灰阀等部位[10-11],漏风严重制约着烧结机产能的发挥与质量的提升。针对以上问题,本文通过现场测量各风箱烟气成分、含氧量变化(图 4)、利用计划检修期间对风箱漏风点进行补焊、风箱喷涂耐磨涂层(图 5)、管道进行更换、台车固定滑道螺栓紧固、台车栏板更换同时加强对台车栏板插销的工艺检查等方式进行相关处的漏风治理。漏风治理后,烧结机上料量提升了 10 t/h,烧结机转鼓强度由 77.66%提升至 78.37%,烧结终点温度提升了 20 ℃ 。
2.2 优化烧结料面布料
550 ㎡烧结机台车栏板高度为 750 mm,在推行厚料层布料后,料层达 920 mm,已超过台车栏板高度 170 mm。在实际生产过程中由于点火炉边缘烧嘴位置不可调,在点火煤气热值波动时极易出现边缘点火效果差,整体边缘效应较为明显的现象。本文通过积极探索,自主改造了一种可调式超烧结机台车栏板压料装置。该装置通过在台车栏板上设置边缘主压料板、斜压板、水平板,使得台车上的料被塑形成梯形,增大了边缘料面的点火,改善了边缘点火、边缘压料等边缘效应。改造后,烧结内返率降低了 1%,产量得到提升,同时边缘料点火效果得到明显改善。压料装置设计、安装、效果图分别如图 6、7、8所示。为减少台面裂痕对烧结矿强度的影响,研发了简易消裂纹装置,消除表面矿由于热胀冷缩产生的应力,简易消除裂纹装置效果如图 9 所示。
3 多工艺协同降低工序能耗效果
550 ㎡烧结多工艺协同实施工序能耗如表 3 所示。结合以上分析与表 3 可知:550 ㎡烧结机单独强化采用低水低碳厚料层烧结、低热值煤气低负压点火、料面喷吹天然气等工艺后,工序能耗分别降低 3.78 、1.44、2.88 kgce/t-s(折标系数分别取 1.01、0.25、1.01); 3种工艺协同使用后,工序能耗降低 7.34 kgce/t-s。虽由于在实际生产中多因素导致该值略低于各工艺单独实施之加和效果,但远高于单独工艺的实施效果。
4 结 论
(1)工序能耗的有效降低不能依靠单一工艺的实施,而需要多工艺协同作用。
(2)550 ㎡烧结采用低水低碳厚料层烧结、低热值煤气低负压点火、料面喷吹天然气等强化烧结工艺后,工序能耗分别降低 3.78 、1.44、2.88 kgce/t-s。
(3)以低水低碳厚料层生产操作为总纲,协同点火炉前移、低负压点火技术改造,烧结料面喷吹天然气为主要工艺方针,通过烧结漏风治理,优化烧结布料等强化辅助措施的实施,可最大幅度地降低烧结工序能耗,由原料的 53.66 kgce/t-s降低到 46.32kgce/t-s。
参考文献:
[1] 杨学斌,李可军. 260m2烧结机节能降耗生产实践[C]//2015 年第三届炼铁对标、节能降本及相关技术研讨会论文集.河北省冶金学会,2015:4.
[1]YangXuebin,LiKejun.Production Practice of Energy Saving and Consumption Reduction of 260m2 Sintering Machine [C]//Proceedings of the 3rd ironmaking benchmarking, energy saving and cost reduction and related technology symposium in 2015. Metallurgical Society of Hebei Province,2015:4.
[2] 曹建刚. 汉钢公司烧结厂降低固体燃料消耗生产实践[C]//第五届全国冶金渣固废回收及资源综合利用、节能减排高峰论坛论文集.河北省金属学会,2020:4.
[2]Cao Jiangang.Production Practice of Reducing Solid Fuel Consumption in Sintering Plant of Hansteel Company [C]//Proceedings of the Fifth National Summit Forum on Solid Waste Recovery of Metallurgical Slag and Comprehensive Utilization of Resources, Energy Conservation and Eemission Reduction. Metal Society of Hebei Province,2020:4.
[3] 顾尚军,陶倩.降低水钢烧结工序能耗的措施[J].能源与节能,2018(2):63-64.
[3]Gu Shangjun,TaoQian.Measures to reduce energy consumption in sintering process of Shuigang[J].Energy and Energy Conservation,2018.02:63-64.
[4] 张永中,曹建民.降低马钢一铁烧结工序能耗的实践[J].烧结球团,[1]张永中,曹建民,卢志武,金龙忠.降低马钢一铁烧结工序能耗的实践[J].烧结球团,2013,38(06):6-10.
[4] Zhang Yongzhong, CaoJianmin.Practice of reducing energy consumption in sintering process of Ma Iron and Steel[J].Sintering and Pelletizing,2013,38(6):06-10.
[5] 李国良,李乾坤.周晓冬.中天钢铁南厂区 180 m2烧结 1#厚料层低负压点火实践[J].冶金信息导刊,2019:12.
[5]Li Guoliang, Li Qiankun. Zhou Xiaodong .Practice of low negative pressure ignition for thick material layer at 180 m2-1# sintering inZenith’ South Iron & Steel Plant[J].Guide to Metallurgical Information,2019:12.
[6] 张俊杰,裴元东,周晓冬.中天钢铁 550 ㎡烧结机喷吹天然气工艺实践[C]//2020 年第八届炼铁对标节能降本及新技术研讨会.河北省金属学会.2020:17-19.
[6] Zhang Junjie, Pei Yuandong, Zhou Xiaodong.Practice of gas injection by sintering machine 550 ㎡ in Zenith’ Iron & Steel Co[C]//The 8th iron making Benchmarking energy-saving and New Technology Seminar .Metal Society of Hebei Province. 2020,2020:17-19.
[7]Oyama N, Iwami Y, Yamamoto T,et al. Development of Secondary-fuel Injection Technology for Energy Reduction in the Iron Ore Sintering Process[J].ISIJ,International, 2011, 51(6):913-921.
[8] 李和平,聂慧远.焦炉煤气强化烧结技术在梅钢的应用[J].烧结球团,2015,40(06):1-3+35.
[8] Li HePing,Nie HuiYuan.Application of coke oven gas intensified sintering technology in Meigang[J].Sintering and Pelletizing,2015,40(06):1-3+35.
[9]叶恒棣,周浩宇.高配比富氢燃料烧结技术研究及展望[J].烧结球团,2020,45(05):1-7.
[9]Ye Hengli,Zhou Haoyu.Research and prospect of high ratio hydrogen - rich fuel sintering technology[J].Sintering and Pelletizing.2020,45(05):1-7.
[10] 刘波,叶恒棣.烧结机低漏风综合密封技术及其在宝钢湛江的应用[J].烧结球团.2018, 43(4):48-53.
[10]Liu Bo, Ye Hengdi.Low air leakage comprehensive sealing technology of sintering machine and its application in Zhanjiang, BaoSteel[J].Sintering and Pelletizing.2018, 43(4):48-53..
[11] 张峰,申理仁.降低烧结机漏风率的制造工艺研究[J].烧结球团,2013,38(05):8-10.
[11]Zhang Feng, Shen Liren.Research on manufacturing technology of reducing air leakage rate of sintering machinel[J].Sintering and Pelletizing.2013,38(05):8-10.