利用盐酸处理炉渣获取有价资源的再循环技术
把钢材在酸洗过程中产生的废盐酸稀释后,将磁选后的炉渣加入稀盐酸溶解槽中,在pH=2-3时进行溶解反应。渣中除有游离CaO之外,铁酸钙和硅酸钙等复合氧化物也较多,但只有Ca成分在数分钟内就选择性溶解成CaCl2,而渣中Fe、Si、Mg等其他金属 氧化物则不溶于稀盐酸,故残渣中Fe含量高即作为铁源留下来。用水洗去残渣中的氯成分后,就可用作炼铁原料进行再循环。
溶解试验表明,若盐酸浓度小于1%,渣中钙的溶出量就少;若盐酸浓度大于5%,除钙以外的铁、硅溶出量就会增多;盐酸浓度为2%-4%时,钙的溶出量多而铁和硅的溶出受到抑制。
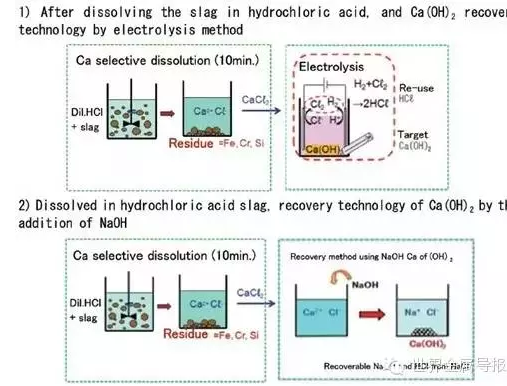
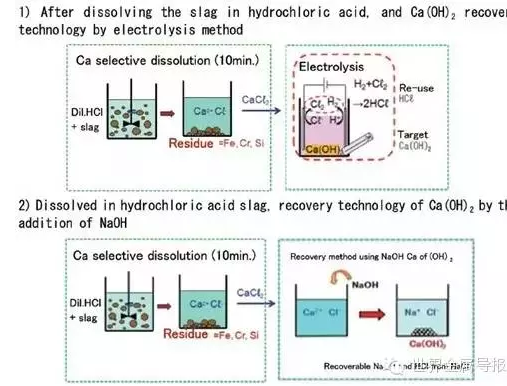
图1 炉渣溶于稀盐酸后的两种Ca(OH)2回收法
如图1上部所示,将分离出的CaCl2溶液直接电解,在阳极上产生Cl2,同时在阴极上生成H2和Ca(OH)2,Cl2和H2通过反应易生成HCl,被稀释后能反复参与炉渣的溶解反应而被再利用。
图1下部所示为在分离出的CaCl2溶液中加入NaOH溶液,进行Ca(OH)2化的技术。通过加入NaOH溶液,将pH值缓慢地从酸性调整为碱性,即pH=3-4时沉淀出Fe(OH)3,pH=5-6时沉淀出Al(OH)3和Cr(OH)3,pH=8-9时沉淀出Fe(OH)2,pH=9-10时沉淀出Mn(OH)2,pH=9.5-10.5时沉淀出Mg(OH)2。故可分阶段将以上沉淀物过滤后,在pH=11-13时获得溶解性低的Ca(OH)2。再用电解处理回收Ca(OH)2后的NaCl溶液,回收NaOH和Cl2(与H2反应为HCl),进行再利用。此技术的特征:一是每次加入少量NaOH时,利用渣中Fe、Al、Cr、Mn、Mg的氢氧化物析出的pH区域不同,较易实现更细的成分分离;二是Ca(OH)2的回收率高;三是将Ca(OH)2分离后的NaCl溶液进行电解,由于回收再利用NaOH和Cl2时的电解电压低,基本上不能在离子渗透膜上形成附着物。
利用3.6%稀盐酸溶解2mm以下渣粒,调查炉渣的成分选择和溶解时间之间的关系。结果表明,10min后渣中Ca成分的溶解比例约达68%,而Ca之外的金属仅有少量溶解。
将投入稀盐酸中的渣粒直径分别控制在0.125mm以下、0.250mm以下、0.500mm以下、5.00mm以下,以相同液固比和反应时间溶解后,求出利用加入NaOH而析出Ca(OH)2的回收率。结果表明,在渣粒径最大的0.500-5.00mm范围,Ca(OH)2回收率低至50%-60%,但其粒径细化到0.250mm和0.125mm时,Ca(OH)2回收率却快速提高到70%和80%。为了避免仅因微细渣的分级对其处理量的限定,有必要在处理渣的破碎成本与Ca(OH)2回收率之间寻找最佳平衡点。
本技术分离回收的Ca(OH)2粉的粒度很细,D50为20μm左右,可以推定1μm以下的实际比例达50%以上,较之市售的消石灰和生灰石,其粒度尺寸要小1-2位数。将回收的Ca(OH)2粉作为烧结黏结剂,无论是在圆盘式或是在滚筒式造球机上的成球比例都很高。