天铁高炉减少风口破损操作实践
谢文飞
(天津天铁冶金集团第一炼铁厂)
摘 要 本文对天铁第一炼铁厂高炉风口破损严重的问题,通过优化配料工作,针对循环物料,均匀配吃,防止配料波动,以自主研发的中型高炉无钟多环布料煤气流转型理论,指导布料操作,突破原有操作模式,全开风口恢复炉况,使高炉风口的破损数目大幅降低,降低了设备的休风率,提升了高炉的经济技术指标。
关键词 高炉;优化配料;多环布料;全开风口;风口破损
1 前言
天津天铁集团第一炼铁厂现有4座700 m3高炉,每座高炉配置16个风口。2011-2013年,累计风口破损642个,低品质料的使用,使烧结矿中的碱金属、Zn升高,导致风口大量破损(见表1)。通过采取各种措施,2014年风口损坏68个。在钢铁市场形势日趋严峻,进一步降低生铁成本过程中取得较好的效果。
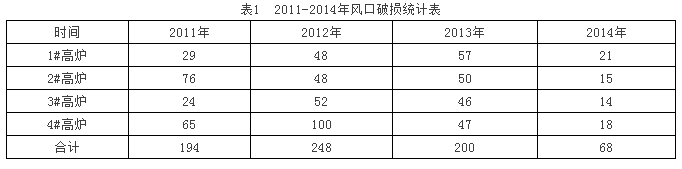
2 风口破损原因
2.1 有害元素含量高
在烧结矿配料方面,考虑低成本因素,混合料配用了布袋灰、烧结机头灰,在烧结矿配矿的比例中,混合料、钢泥配加比例较大,使烧结矿中的碱金属、Zn含量升高,高炉碱负荷、锌负荷较重。2011-2013年锌负荷最高达到0.8kg/t。一方面碱金属造成焦炭粉化,Zn在炉缸大量吸热,使炉缸向凉,透液性和透气性变差,造成高炉出现排碱、排Zn现象频繁,导致风口大量破损;另一方面,碱金属和锌渗入炉衬中,导致砖衬膨胀,炉体长高、长胖,导致风口及二套变形、上翘。
2.2 高炉上下部调剂
由于外部条件变化,上部调整装料制度不到位,导致中心或边缘气流过于旺盛或不足,造成渣皮脱落,使炉缸透液性大幅下降,炉缸的工作状态变差,不活跃,死区较多,炉缸堆积现象较为频繁,易造成风口大量破损。
2.3 高炉休风恢复炉况
高炉生产中60天左右需要一次10-12小时的定修,在恢复炉况过程中,均采取花堵3~4个风口。目的是为了维持适宜的风速及鼓风动能,保证吹透中心,以快速恢复炉况。每次炉况恢复的过程中,都出现堵泥风口两侧的风口损坏,每次破损风口3-5个,甚至出现风口二套烧坏,需要组织休风更换。
2.4 渣皮脱落
由于原燃料质量变化或大量使用焦丁后,使高炉煤气流发生变化,导致炉墙渣皮脱落,富集在局部风口处,使风口烧坏。
3 采取的措施
3.1 优化配料工作
3.1.1 燃料控制
由于焦炭入库后存放时间较长,没有及时使用,造成强度降低,造成炉况波动风口损坏。根据入库时间,季节特点,合理安排出库。及时了解焦炭配煤比的变更情况,加强热强度、水分的监控。及时调整焦比、煤比,确保炉况稳定。
针对部分酸性球团含钛偏高,造成渣铁粘稠,类似炉缸堆积的情况,采取要求供应商提供的球团钛含量小于0.04%。在给高炉取料时,将含钛偏高的球团与含钛低的球团各取50%,进行混合后供给高炉,同时将高炉球团的配加比例控制在10-15%,降低了渣铁的粘度,提高了渣铁的流动性。
第一炼铁厂长期使用南非块矿,由于南非块矿冶金性能较好,但碱金属含量较高,钾含量在0.25-0.35%,钠含量0.13%左右。针对块矿长期使用南非块矿,品重单一的情况,采取拓宽块矿的品种,配加了麦克块、纽曼块、恰那块、PB块等有害元素含量低的块矿品种。块矿配加比例控制在17%左右,既确保了高炉炉况稳定顺行,又减少了碱金属的带入量。
通过配料技术控制有害元素的含量,要求锌负荷<0.5kg/t,碱负荷K2O+Na20≤3.5kg/tFe。针对碱金属含量高的烧结机头灰不再直接配吃,与锌含量高的布袋除尘灰合并流程,经脱除锌、钾、钠等有害元素后再回混匀料堆,根据循环物料的产量,均匀配吃,防止配料波动。对含锌高的干钢泥的配加由5%调整到3%,既保持了经济料的使用,又降低了高炉炉料的锌负荷,避免了干钢泥集中配加带来的锌负荷急剧升高,造成的炉况失常;烧结矿的白云石的配加量由8%提高到8.5%,高炉炉渣的镁铝比由0.63%提高到0.65-0.68%的范围,镁铝比提高以后,使高炉的排碱、排锌的能力得到提高,稳定的碱负荷、锌负荷使高炉炉况平稳,降低了风口的破损。
3.2 通过炉况调剂,保持合理的操作炉型
在焦丁的使用上,我们对配加焦丁发展边缘气流的作用没有得到充分的重视,配加焦丁后3-5天后出现炉墙渣皮脱落,造成炉凉,炉缸渣铁透液性急剧下降,造成焦比上升,风口频繁损坏。因此在使用焦丁时,装料制度采用适度加重边缘的措施。向边缘加一圈矿或减一圈焦,或布料角度调整0.5°等措施,使高炉布料平台中心和边缘的矿焦比保持稳定,确保了中心和边缘气流的稳定,进而稳定了炉墙渣皮。确保了炉况的长周期稳定顺行,减少了风口的损坏。采用此项措施后,未再出现吃焦丁后渣皮脱落、风口损坏情况的发生。
通过调剂布料制度,在边缘气流过旺的情况下,采取向边缘增加布矿的环数或减少布向边缘焦炭的环数,增加布向中心的焦炭比例;情况较严重时,调整布矿或布焦的角度0.5-1度;根据焦炭质量和落地矿的多少调整矿石和焦炭的批重。3-5个冶炼周期煤气流转型后,再巩固效果。以自主研发的中型高炉无钟多环布料煤气流转型理论,指导布料操作。通过以上的调剂手段,使中心气流狭长而锐利,边缘气流通畅,形成一个狭窄的边缘通路,使中心气流强于边缘,达到合理的煤气流分布,煤气利用率由36%-39%提高到42-44%,使操作炉型规整,使炉墙渣皮保持相对稳定,保持炉缸工作正常活跃,炉缸的透液性良好,使风口的工况条件改善,避免局部窝渣、窝铁现象。
在下部调剂中,由于第一炼铁厂高炉风口布局,原来为直径120mm×3+110mm×13配置,风口面积0.1574m2,配置不够理想。后来逐步调整到直径110mm×16个,面积0.1520m2,配置较为均匀但风口面积又相对偏小,炉缸边缘存在死区;经过计算、研究、探讨、比对,根据各高炉不同的风机能力,扩大风口面积,三高炉风口面积由0.1520m2扩大到0.1573m2,其中6个风口直径由100mm扩大到115mm;一、二高炉风口面积由0.1520m2扩大到0.1555 m2,各有4个风口直径由100mm扩大到115mm,风量提高了100-150m³/min。风口面积适度扩大后,减少了炉缸死区,活跃了炉缸边缘,使得渣铁的流动性得到较大改善。
炉缸热制度不稳定,化学热和物理热波动较大。通过高炉日常操作中严格控制生铁含硅[Si]在0.25%-0.45%之间,炉温的稳定率(0.25%-0.45%之间)由56%提高到80%左右,铁水物理热保持在1480℃左右,炉缸的热制度充沛稳定。
3.3 采用快速恢复炉况技术
经过研究,在高炉长期休风后的恢复过程中,根据渣铁环流理论和操作实际,针对现有的工况条件,对原有的操作方式,进行了大胆革新,采用全开风口作业,快速提高风量,依靠大风量增大鼓风动能。保证了炉况恢复过程中初始煤气流分布合理,避免了由于高风压条件下,堵风口作业造成的对炉缸圆周渣铁环流的阻断作用,基本杜绝了此种情况下风口的熔烧破损。
复风初期,为确保料动,且尽快形成煤气流,抓住时机,积极稳妥用风。送风后根据压量关系在30~60分钟左右将风压加至160kPa左右,压差维持在90~100kPa。在风量偏大时,压差控制在80~90kPa。用较低的压差,提高高炉煤气流的稳定性,减少崩塌料、悬料的产生,缩短恢复时间。下料后逐步赶料线。
风量加至正常风量的80%,则放缓加风节奏,一方面稳定气流;另一方面,防止炉温大幅下跌,进而影响料尺正常动作,形成崩、悬料。随煤粉作用,热量回升,逐步加全风量。复风初,由于重建煤气流,尤其在O/C比较高的高炉,前期风压高,风量小,透气性差,不吃风。而对于大型高炉,风量达不到一定水平,风口前料不动,而此时,不能因为憋压、高压就不加风。
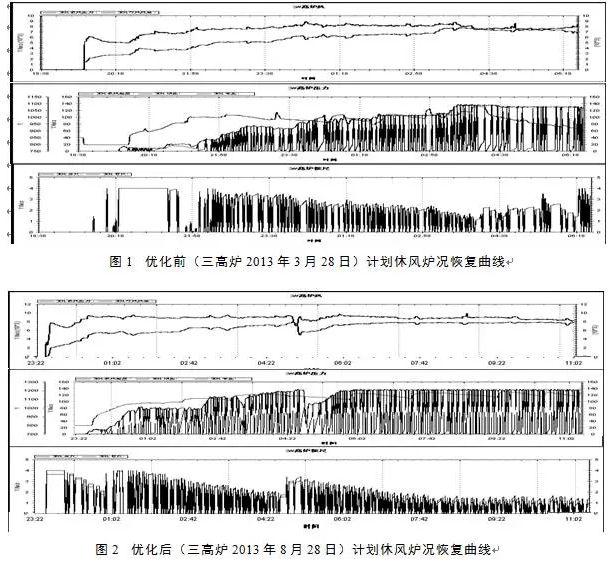
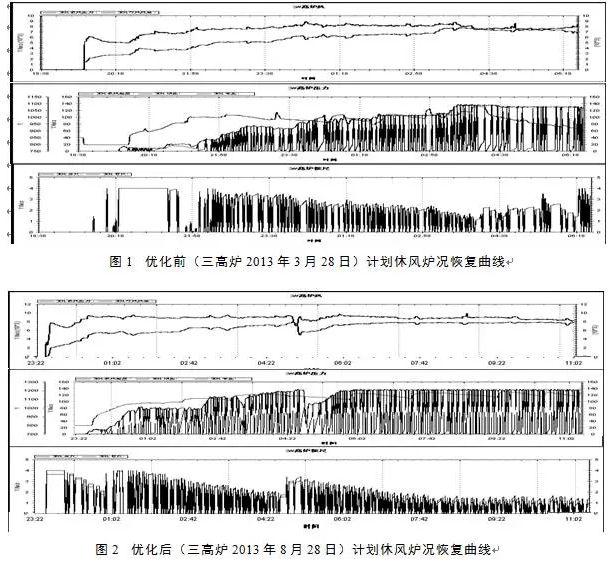
优化操作前后送风曲线和送风风压、风量、顶压变化见图1、图2。
该技术推广后,每次长期休风炉况恢复时间由2-3天缩短到7小时左右;风口基本无损坏。通过表2、表3、表4,优化后(如2013年8月28日)三高炉计划休风及恢复期间与优化前(如2013年3月28日)三高炉计划休风及恢复期间指标对比,综合焦比降低66.78kg/t,减少焦炭量360.58t,产量增加近1955t。2013年3月28日三高炉计划休风及恢复期间损坏风口3个,二套1个,二次休风即30日8:35~11:50更换损坏的风口及二套,直到30日风口全开,炉况恢复正常,增加了炉况恢复到正常的时间。
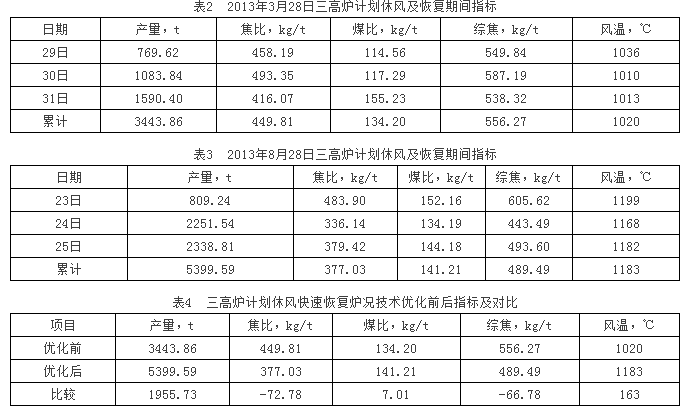
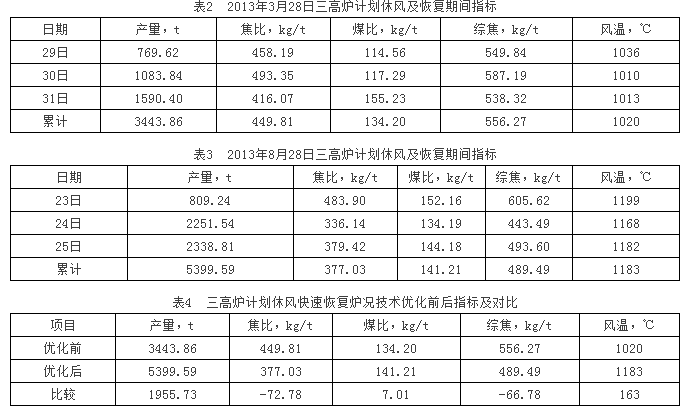
4 实施效果
通过优化配料工作,炉况调剂保持合理的操作炉型,快速恢复炉况技术等措施,烧结矿碱金属K2O含量由0.15%下降到0.10%,Na2O含量由0.05%下降到0.04%。重力除尘灰碱金属K2O含量由0.58%下降到0.33%,Na2O含量由0.79%下降到0.14%,Zn含量由1.8%下降到0.43%。高炉经济技术指标得到了大幅提升(见表5),2014年综合焦比下降到511.43kg/t,休风率由3.59%下降到2.82%,风口破损数目由2012年的273个(月平均损坏22.75个),2013年的202个(月平均损坏16.83个),下降到2014年68个(月平均损坏5.67个),取得显著效果。
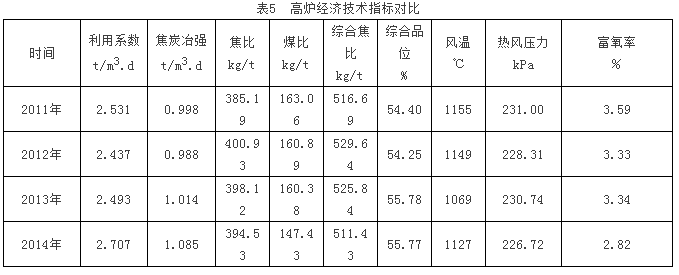
5 参考文献
[1] 由文泉.实用高炉炼铁技术[M].北京:冶金工业出版社,2004.350-351.
[2] 周传典.高炉炼铁生产技术手册[M].北京:冶金工业出版社,2008.443-451.